Timber Structures 3.0: Holzbauteile stirnseitig verklebt
Das Start-up Timber Structures 3.0 AG hat zusammen mit der Berner Fachhochschule eine neue Technologie entwickelt, die es erlaubt, Holzbauteile stirnseitig zu verkleben. So sind punktgestützte, mehrachsig tragende Platten oder Faltwerke in jeder Form möglich. Geschossdecken können nun aus Holz gefertigt werden.
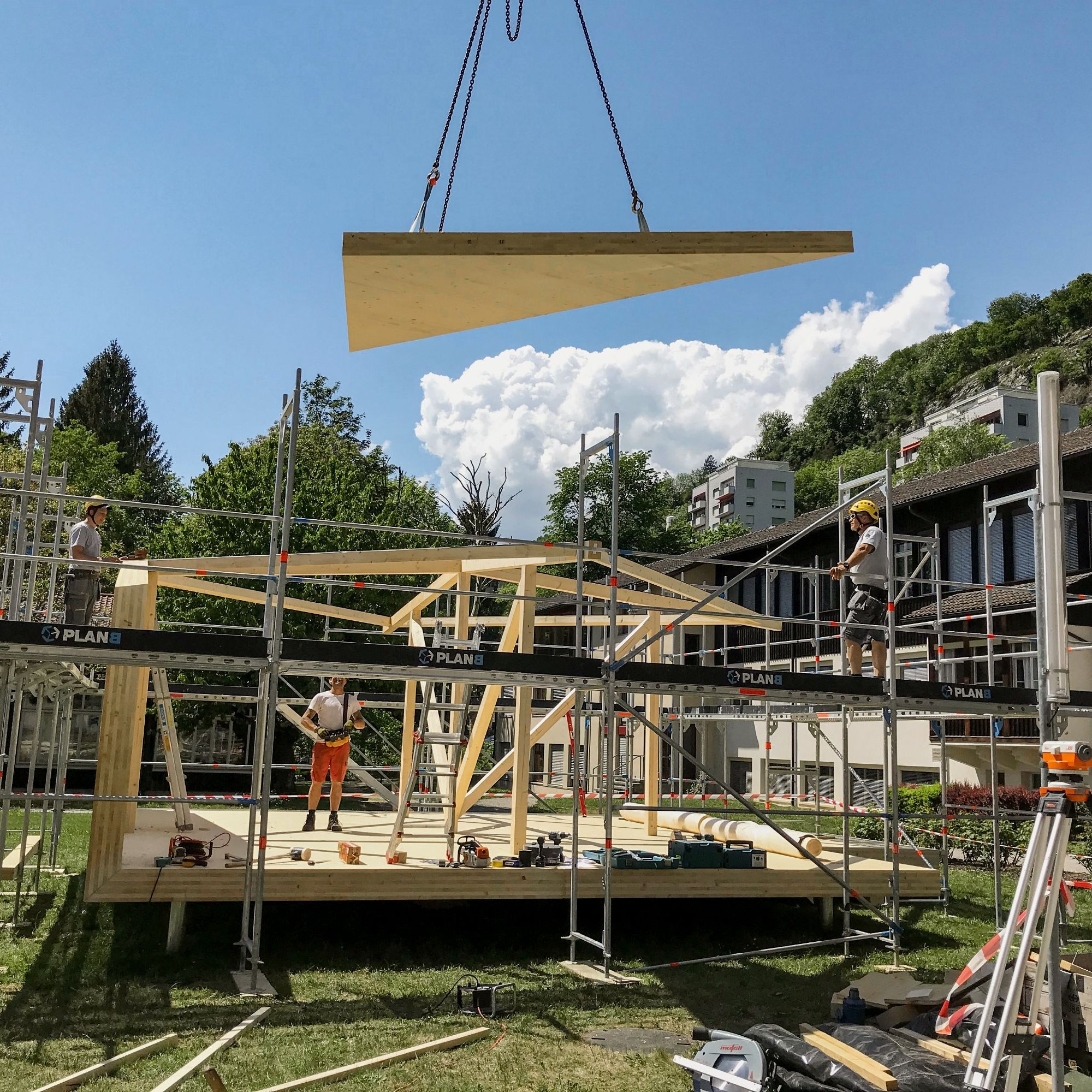
Quelle: Steffen Franke
Das erste Dachelement wird auf das Lehrgerüst versetzt. Die Decke und Wand sind bereits verklebt und ohne Abstützungen.
Von Karin Stei
Frust kann lähmen oder beflügeln. Im Fall von Stefan Zöllig ist es Letzteres, das zu einer bahnbrechenden Innovation im Holzbau geführt hat. Der Gründer der Timbatec Holzbauingenieure Schweiz AG entscheidet sich 2009, ein grosses Problem des Holzbaus in Angriff zu nehmen. Da Holz im Gegensatz zu Beton nur in einer Richtung trägt, müssen Holzdecken durch Unterzüge und viele Stützen getragen werden. Diese massiven Träger behindern die Installation von Haustechnik und Nutzungsänderungen und kosten wertvollen Raum. «Als Holzbauingenieur verbaut man deshalb Stahlträger und Beton.
Wir haben damals ein Gebäude erstellt, in dem 2000 Tonnen Beton, 500 Tonnen Stahl und 500 Tonnen Holz verbaut wurden und es einen Holzbau genannt. Eine Materialkombination, die viele Nachteile hinsichtlich Gewicht, Bauzeit, Kosten und Ökologie aufweist. Da ist mir die Lust vergangen», erklärt Stefan Zöllig. Zusätzlich frustrierend ist, dass Ausschreibungen bei Gewerbeobjekten aufgrund der Stützenproblematik nicht gewonnen werden.
«Stütze, Platte, fertig»
«Stütze, Platte, fertig», bringt Zöllig seine Idee eines neuen Holzbausystems (TS3) auf den Punkt. Er will einen Skelettbau mit einem Stützenraster von acht auf acht Metern und einer Nutzlast von 500 Kilogramm pro Quadratmeter mit flachen, zweiachsig tragenden Decken erstellen. Die grösste Herausforderung: Es muss eine Lösung für die stirnseitige Verklebung von Holzplatten gefunden werden. Denn nur so lassen sich zweiachsig tragende Deckenkonstruktionen in beliebiger Grösse herstellen, die Betondecken ersetzen können. Zöllig findet dafür Partner in Forschung und Wirtschaft mit dem Institut für Holzbau, Tragwerke und Architektur der Berner Fachhochschule (BFH) in Biel, der Eidgenössischen Technischen Hochschule in Zürich (ETH), der Schilliger Holz AG als Säge- und Plattenwerk und der Henkel & Cie. AG als Klebstoffhersteller.
«So eine Technologie wurde für unmöglich gehalten. Alle Praktiker waren sich einig, dass eine verklebte Stirnholzverbindung nicht hält, und wir wurden anfangs dafür belächelt», erzählt Steffen Franke von der Berner Fachhochschule (BFH) in Biel. Der Professor für Holzbau und Statik stösst 2011 zum Projekt, das ihn aufgrund des hohen Innovationspotenzials reizt.
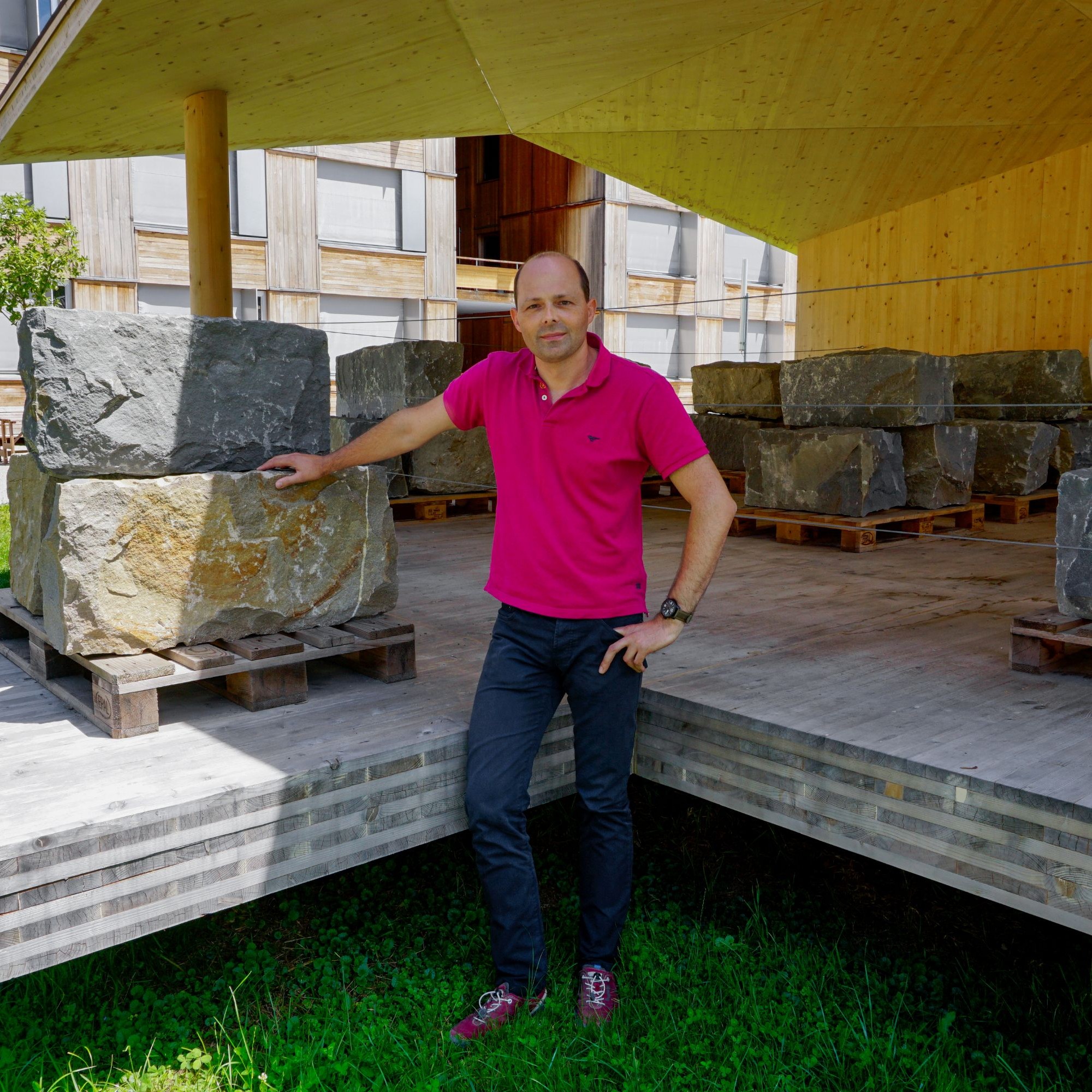
Quelle: Karin Stei
Steffen Franke beim TS3-Dauerprüfstand im Innenhof der Berner Fachhochschule in Biel.
Tests an BFH und ETH
Die Forschungen werden zu Beginn durch den Fonds zur Förderung der Wald und Holzforschung des Bundesamts für Umwelt unterstützt, von 2016 bis Februar 2020 finanziert die Kommission für Technologie und Innovation (KTI), heute Innosuisse, das Projekt. Neun Master- und zehn Bachelorarbeiten entstehen während der Entwicklung, über 1800 Biege-, Zug- und Drucktests finden an der BFH und ETH statt. Studien zu Feuchtigkeitsveränderungen, Langzeitbelastungen, zur Zug- und Biegefestigkeit der stirnseitigen Verbindung sowie auf Brandverhalten wurden durchgeführt.
ETH und BFH teilten sich die Aufgaben. So übernahm die ETH die Entwicklung des Stützenkopfs, auf den besonders grosse Kräfte einwirken, des Brandschutzes und des Gesamttragwerks. Das Resultat jahrelanger Forschung kann sich sehen lassen. Hochfeste, speziell geschichtete Stützenköpfe erreichen je nach Deckenstärke und Aufbau Bruchlasten von 1100 bis 3100 Kilonewton (110 bis 310 Tonnen). Damit die Platten in beiden Richtungen die gleiche Steifigkeit haben, wurden asymmetrische Brettsperrholzplatten entwickelt.
An der BFH beschäftigten sich Franke und sein Team intensiv mit der stirnseitigen Verklebung und der «GridBox», einem zweiachsig tragenden Hohlkasten mit Trägerrost-Innenleben. «Die Festigkeit der Fuge war die grosse Herausforderung», sagt Franke. Anfangs experimentierte man mit einer Keilzinkenverbindung, um die Platten zusammenzufügen. «Wir verklebten Teile mit gefrästen Keilzinken auf Abstand.

Quelle: Steffen Franke
Biegeprüfung der Fuge der angeklebten Balkonplatte anhand eines 20 Zentimeter breiten Streifens (links). Verguss der abgedichteten Fuge der Deckenplatten (rechts).
Diese Art der Verbindung erwies sich jedoch schnell als zu aufwändig. Die Risse zeigten sich immer an den Zinkenspitzen. Als wir die Platten testhalber stumpf verklebten, erreichten wir bereits eine relativ gute Festigkeit, und es zeigte sich, dass die Keilzinken gar nicht nötig waren. Diese stumpfe Fuge kann nun zwischen vier und 20 Millimetern stark sein, getestet haben wir sie sogar bis 40 Millimeter», berichtet Franke. Die Zugfestigkeit der Verklebung erreicht heute Werte im Mittel bis über 15 Newton pro Quadratmillimeter.
Ein Problem stellte die Blasenbildung beim Einfüllen des Klebstoffs in der Fuge dar. Versuchsreihen zeigten, dass die unerwünschte Blasenbildung durch spezielle Vorbehandlungen des Brettsperrholzes, unter anderem durch Schleifen und einen im Werk aufgetragenen, modifizierten Klebstoff, vermieden werden konnte. Der formaldehydfreie Zweikomponenten-Polyurethan-Klebstoff von Henkel & Cie. AG war durch das Einkleben von Gewindestangen erprobt und wurde während der Entwicklung modifiziert.
«Der Klebstoff wird auf der Baustelle in die Fuge von unten injiziert. Über eine zweite, obere Bohrung, oder durch kleine Löcher im Klebeband, das zur Abdichtung aufgeklebt wird, findet die Entlüftung statt», erklärt Steffen Franke und ergänzt: «Nach zwei Tagen ist die Fuge zu 80 Prozent belastbar, die volle Tragfähigkeit ist nach zehn Tagen gegeben. Das bedeutet eine grosse Zeitersparnis beim Bauen.» Ersparnis bringt auch die parallel entwickelte «GridBox». Sie kann bei grösseren Decken, die dann noch beschwert sein müssen, eingesetzt werden.
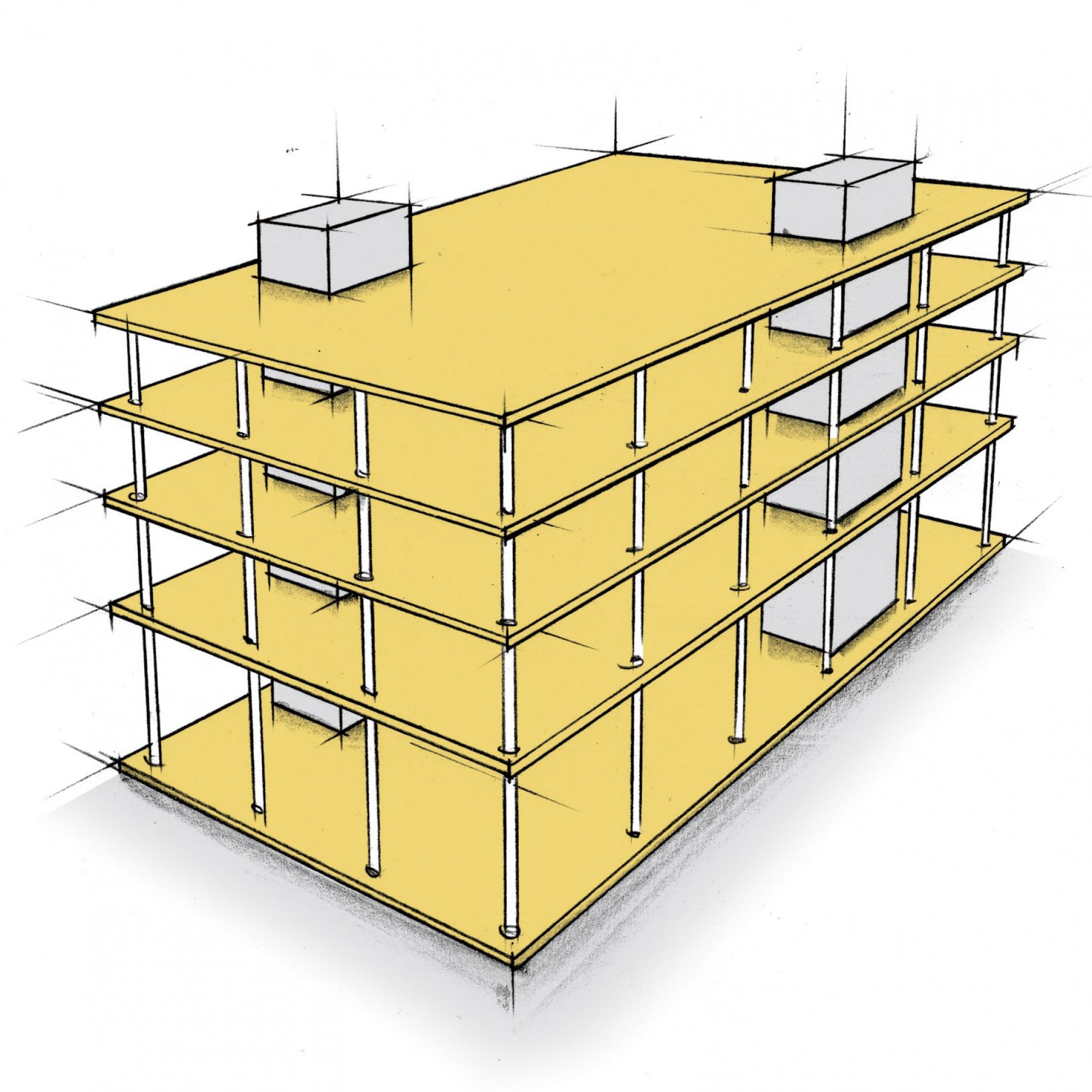
Quelle: TS3 AG
Die neuen Technologien ermöglichen es, flächig tragende Bauteile aus Holz für Geschossdecken zu bauen.
Zwei Prüfstände
An zwei Prüfständen wurde das neue System, benannt «Timber Structures 3.0», getestet. 2017 errichtete man an der ETH einen Prüfstand, der aus vier miteinander verklebten Brettsperrholzplatten bestand. Das Dach wurde nach der Erstellung mit zwölf Big Bags belastet, deren 9,6 Tonnen Gewicht ein Jahr auf der Decke lasteten. Damit wurden die quasi-ständigen Lasten einer Decke simuliert, welche eine Nutzlast von bis zu 500 Kilogramm pro Quadratmeter zulässt. Der Prüfstand ist heute abgebaut und wird im Herbst 2019 an der Materialprüfungsanstalt Universität Stuttgart wieder aufgestellt.
Der Prüfstand in Biel wurde 2018 als weiterer «Proof-of-Concept» und Demonstrationsobjekt gebaut. «Wir haben sogar eine Delegation aus Japan hier gehabt, die sich von TS3 überzeugen wollte», berichtet Franke. Zu sehen ist eine punktgestützte, zweiachsig tragende Geschossdecke, die aus acht Brettsperrholzplatten besteht und durch den stirnseitigen Klebeverguss zusammengefügt wurden. Belastet wurde hier die Bodenplatte mit zwölf Tonnen schweren Steinblöcken, was einer Dauerflächenlast von fünf Kilonewton pro Quadratmeter entspricht.
Eine Weltneuheit ist die einzelne aussteifende Wandscheibe, die mit der Bodenplatte biegesteif unter 45 Grad ebenfalls stirnseitig verklebt wurde. «Normalerweise braucht man für die Aussteifung drei Wände», erklärt Franke. Das Dachtragewerk wurde aus acht Brettsperrholzelementen in Dreiecksform unter unterschiedlichen Neigungen gebildet. Ausserdem gelang es das erste Mal überhaupt, eine voll belastbare Balkonplatte direkt anzukleben.
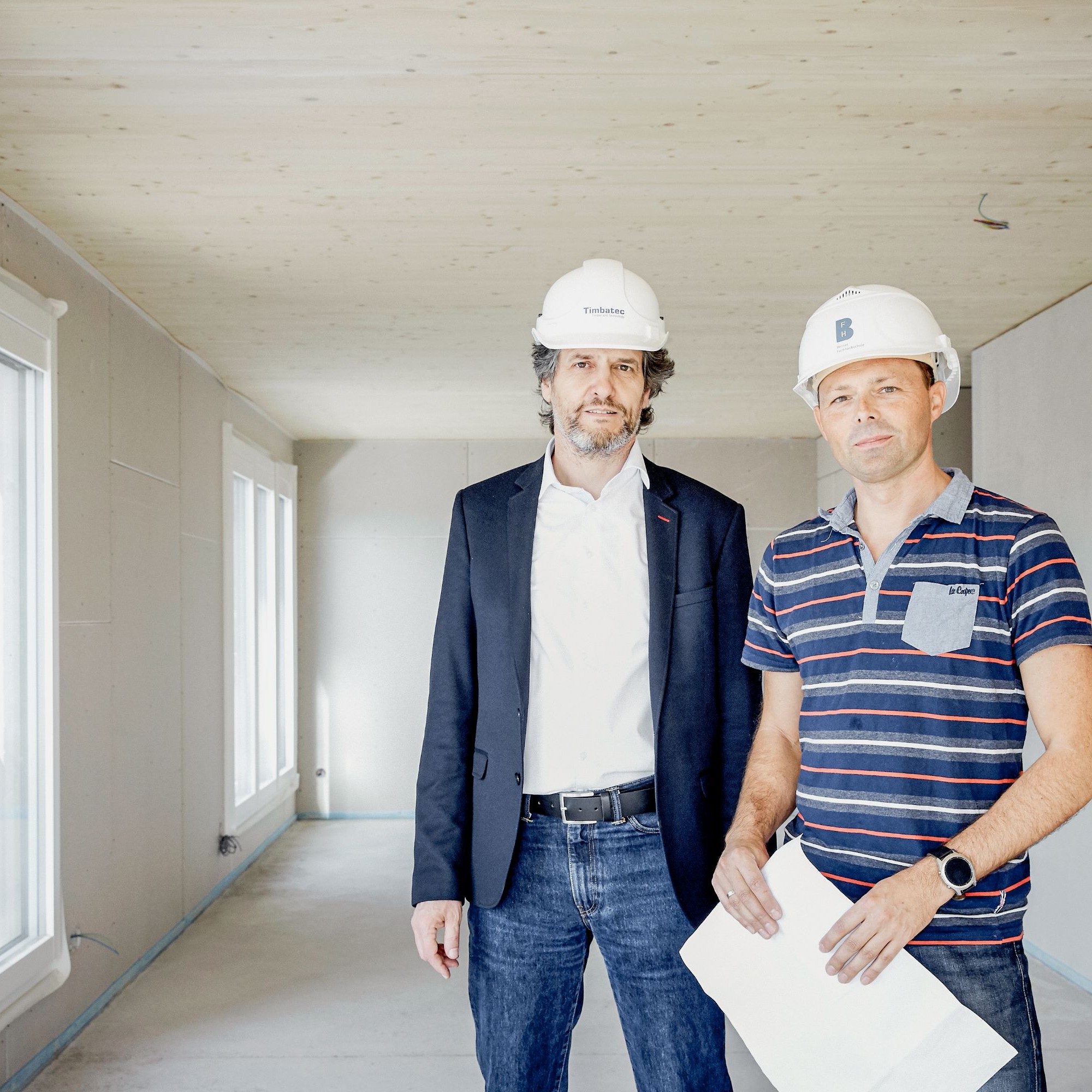
Quelle: Bild: BFH
Stefan Zöllig (links) und Steffen Franke auf der Baustelle in Grossaffoltern. Hier wurde die Geschossdecke mit der neuen TS3-Technologie hergestellt.
Forschung geht weiter
Die Prüfstände brachten Erkenntnisse über den Montage- und Vergussprozess, das Verformungs- und Schwingungsverhalten. Und vor allem zeigten sie: TS3 funktioniert. Damit können nun erstmals flächig tragende Holzelemente gefertigt werden, die die Konstruktion von punktgestützten Holzflachdecken mit einem Stützenraster bis acht mal acht Meter und einer Nutzlast von fünf Kilonewton pro Quadratmeter erlauben. Weitere Forschungen werden sich laut Franke unter anderem mit den Faltwerken, der Robustheit und Erdbebensicherheit beschäftigen. «Die Fuge ist per se leider spröde, was sich negativ auf die Erdbebensicherheit auswirkt, aber man muss immer das Gesamtbild sehen. Es geht jetzt darum, alternative Lösungen für ein robustes System zu finden.»
Dieser Erfolg führt 2014 zur Gründung des Start-ups Timber Structures 3.0 AG durch Stefan Zöllig in Thun. Nur ein Jahr später wird das erste Mehrfamilienhaus mit der TS3-Technologie in Thun gebaut, vier Mehrfamilienhäuser entstehen 2018 in Grossaffoltern. Momentan stehen drei konkrete Projekte an: ein Hortgebäude in Schlieren, bestehend aus drei runden Pavillons, zwei Mehrfamilienhäuser mit jeweils acht Wohnungen am Zollikerberg und ein Mehrfamilienhaus mit 20 Wohnungen in Frenkendorf.
Die Holzbauingenieure von TS3 braucht man von ihrer neuen Technologie nicht zu überzeugen. Schwieriger ist es, diese Innovation in den Markt zu bringen. Anvisiert hat Zöllig vor allem zwei Absatzgebiete – Europa und Nordamerika mit den USA und Kanada, da sie über eine Holzbaukultur verfügen. Die Zulassung in den USA und in der EU ist beantragt und wird gegen Ende 2020 erwartet.
Bis dahin ist eine Zustimmung im Einzelfall erforderlich. In der Schweiz braucht es keine Zulassung. Deshalb wird viel in der Schweiz entwickelt und erprobt, bevor man sich an den teuren und langwierigen Zulassungsprozess macht. «Wir sind auf Messen und Kongressen präsent, halten Vorträge, um uns bekannter zu machen und haben sehr gute Beziehungen in den USA und Kanada aufgebaut», freut sich Zöllig.
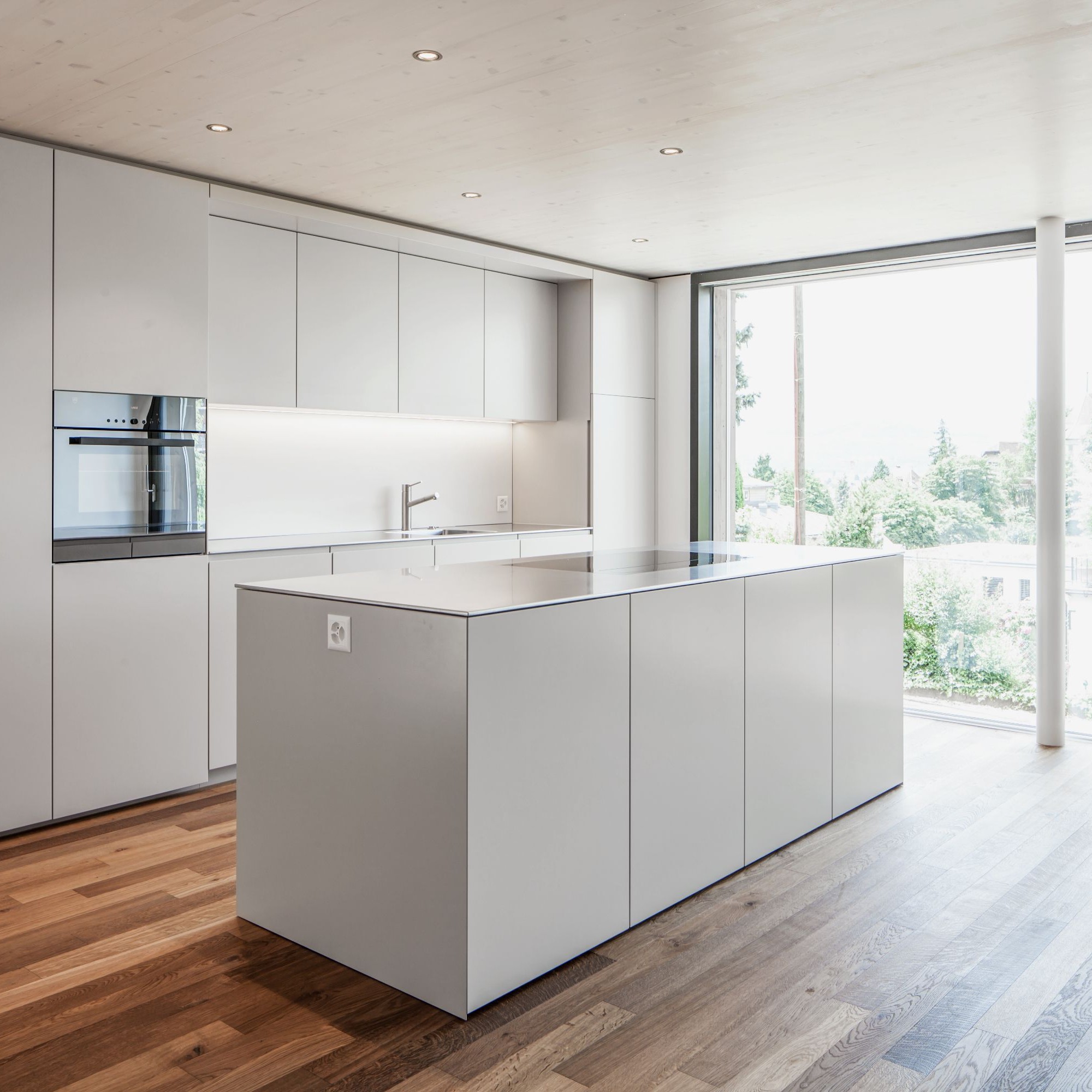
Quelle: TS3 AG
In Thun wurde 2015 das erste Mehrfamilienhaus mit der TS3-Technologie gebaut.
Anwendungstechniker ausgebildet
Ein weiterer Verbreitungsweg besteht in der Schulung von Anwendern als Lizenznehmer. Im Januar 2019 wurden in Vancouver vierzehn Anwendungstechniker aus den USA und Kanada ausgebildet. In Zukunft soll dies per E-Learning geschehen. «Wir haben eine Box mit allen nötigen Materialien zusammengestellt. Anhand eines Videos muss uns der Anwender zeigen, ob er die Technik beherrscht und erklären kann, um das Zertifikat zu erhalten.»
Wichtig ist Zöllig die konsequente Qualitätssicherung. So haben die Erkenntnisse aus der Forschung zu einer Optimierung und Verfeinerung der Methoden und Prozesse bei der Fertigung und Montage geführt, die von den Produktionsfirmen in Lizenz durchgeführt werden. Von der Verwendung eines geeigneten Klebebandes bis hin zum Einsatz von Verklebungsgeräten statt Kartuschen auf der Baustelle reichen die Innovationen.
Momentan steht die Industrialisierung im Fokus. Um die mit Rillen und Entlüftungslöchern ausgestatteten Brettsperrholzplatten in grossem Massstab vorbehandeln zu können, arbeitet Zöllig mit CNC-Maschinen-Produzenten und Klebstoffherstellern zusammen, um ein Gerät zu entwickeln, das sich direkt auf der CNC-Maschine anbringen lässt und so die manuelle Vorbehandlung ersetzt.
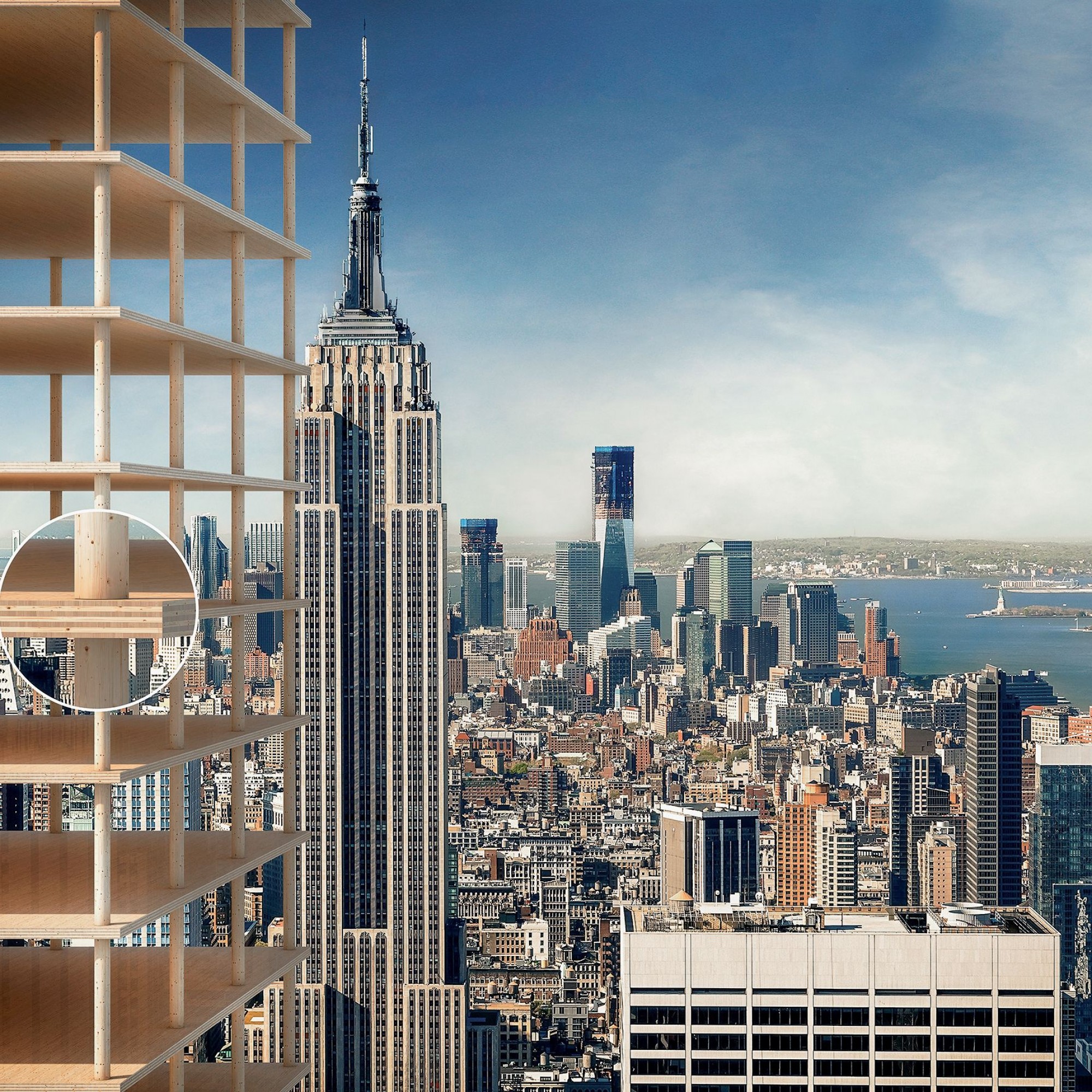
Quelle: TS3 AG
Sogar Hochhäuser aus Holz sind mit der neuartigen TS3-Technologie möglich. Die vertikalen Lasten werden direkt auf die Stütze abgeleitet.
Grosses Potenzial
Nicht von ungefähr haben Zöllig und sein Team an den Namen Timber Structures den Zusatz 3.0. angefügt. «TS3 ist die dritte Generation im Holzbau. In der ersten Generation haben wir nur Bäume bearbeitet, dann in der zweiten Generation durch Brettschicht- und Brettsperrholz neue Möglichkeiten erschlossen. Die stirnseitige Verklebung eröffnet jetzt ganz neue Dimensionen, unter anderem durch die höhere Nutzungsflexibilität und die Vielgeschossigkeit. Wir haben bisher drei Patente und sieben Technologiefamilien entwickelt, aber da steckt noch viel mehr Potenzial drin», ist der Holzbauingenieur überzeugt. «Momentan hat der Holzbau laut Schätzungenim Markt einen Anteil von 10 Prozent, wir sind an den restlichen 90 Prozent interessiert.»
Ökologische Vorteile
Vor allem in den Städten erwartet Zöllig einen grossen Holzbauboom. Mit Holz lässt sich schnell, sauber, trocken und wirtschaftlich bauen und, vor allem wichtig in heutigen Zeiten, nachhaltig und klimafreundlich. «Holz bindet CO2, dagegen belasten der Stahl- und Betonbau die Umwelt. Die Zementindustrie wird für rund neun Prozent des weltweiten CO2-Ausstosses verantwortlich gemacht. Unsere Innovation bietet Baufirmen, die bisher mit Stahl und Beton gearbeitet haben, die Chance, neue Wege einzuschlagen», versichert Zöllig.
Weitere Informationen: www.ts3.biz
www.bfh.ch/de/forschung/referenzprojekte/ts3
https://frangi.ibk.ethz.ch