Verfahrenstechnik: Neue Rezepte für Stahlkocher
Die Produktion von Stahl verursacht rund acht Prozent der weltweiten Emissionen von Kohlendioxid. Fraunhofer-Institute arbeiten daher zusammen mit Industrieunternehmen an der Dekarbonisierung des Herstellungsprozesses. Konkret geht es dabei um die Direktreduktion von Eisenerz mit Wasserstoff. Auch Forschungen am Karlsruher Instituts für Technologie streben eine Modernisierung bestehender Hochofentechnologien an. Die Umrüstung soll bei moderaten Investitionen möglich sein.
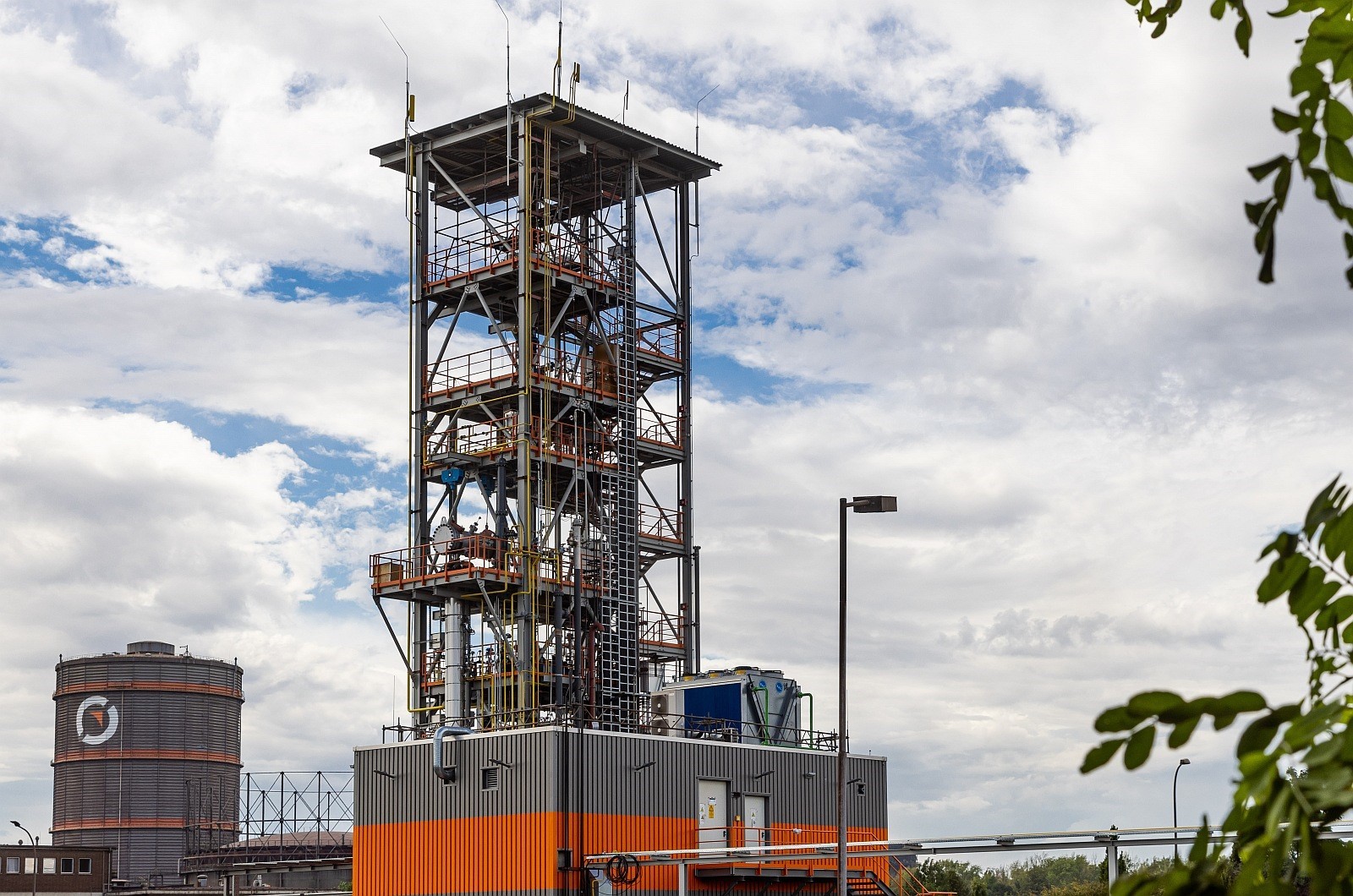
Quelle: Salzgitter AG
μDRAL-Anlage – erste flexibel mit Wasserstoff und Erdgas betriebene Direktreduktionsanlage in einem integrierten Hüttenwerk.
Stahl ist ein Material mit vielfältigen Qualitäten. Neben Baustahl findet er in nahezu allen Produkten Verwendung, in denen es auf Eigenschaften wie Festigkeit, Verformbarkeit und Stabilität ankommt. Der Einsatz von Stahl bei Gebäuden, Fahrzeugen, Maschinen oder Haushaltsgeräten macht ihn daher unverzichtbar. Doch laut Angaben des Kompetenzzentrums Klimaschutz in energieintensiven Industrien (KEI) werden bei der Stahlherstellung allein in Deutschland gesamthaft pro Jahr etwa 55 Millionen Tonnen Kohlendioxid emittiert. Die Stahlindustrie verursacht damit rund 28 Prozent der gesamten Kohlendioxid-Emissionen der deutschen Industrie. Verursacht werden die Emissionen in erster Linie durch den Einsatz von Koks.
Direktreduktion mit Wasserstoff
Um die Produktion zu dekarbonisieren, werden daher seit Jahren neue Technologien erforscht. Das Fraunhofer-Institut für Keramische Technologien und Systeme (IKTS) sowie die Partnerinstitute in den Bereichen der System- und Innovationsforschung (ISI) und der Umwelt-, Sicherheits- und Energietechnik (UMSICHT) setzen in Zusammenarbeit mit der Salzgitter AG bei ihrem Forschungsansatz auf die Direktreduktion auf Basis von Wasserstoff, wie die an der Forschung beteiligten Parteien in einer Mitteilung schreiben. Bei der Direktreduktion in einem Reaktor reagiert Eisenerz bei hoher Temperatur mit Wasserstoff. Dieser dient als Reduktionsmittel und entzieht dem Eisenerz das Eisenoxid. Zurück bleibt der Rohstoff Eisen.
Doch um das bereits bekannte Produktionsverfahren klimaneutral ausgestalten zu können, muss der Wasserstoff aus erneuerbaren Energiequellen stammen, die den Strom für die dazu benötigte Elektrolyse erzeugen. Mit der Direktreduktion ist der vollständige Verzicht auf das klimaschädliche Koks verbunden. Es dient bei herkömmlichen Produktionsprozessen für Stahl als Reduktionsmittel und liefert dafür die nötige Energie. Wird der Strom aus erneuerbaren Energiequellen bezogen, ist die Herstellung von Wasserstoff vollständig emissionsfrei, wie das Fraunhofer-Institut in einer Mitteilung schreibt. Unter Einsatz von grünem Wasserstoff kann gemäss Matthias Jahn, dem Abteilungsleiter Energie- und Verfahrenstechnik am Fraunhofer IKTS, bei der Rohstahlherstellung bis zu 97 Prozent des klimaschädlichen Kohlendioxids vermieden werden.
Grün mit Hochtemperatur-Elektrolyse
Grundsätzlich wird sogenannter grüner Wasserstoff über Elektrolyseverfahren erzeugt, in dem eine elektrische Spannung angelegt wird, wodurch Wasserdampf in Wasserstoff und Sauerstoff aufgespalten wird. Das Fraunhofer IKTS setzt auf eine Hochtemperatur-Elektrolyse auf Basis von Festoxid-Zellen (englisch: SOEC - Solid Oxide Electrolyzer Cell). Diese Vorgehensweise hat im Gegensatz zu anderen Elektrolyseverfahren, insbesondere bei der Stahlproduktion, erhebliche Vorteile, da die Abwärme aus den Hochtemperaturprozessen genutzt werden kann und damit der elektrische Wirkungsgrad erhöht wird. Die Forscherinnen und Forscher am Fraunhofer IKTS haben eigene Elektrolysezellen und -stacks entwickelt und für die techno-ökonomische Bewertung des Verfahrenskonzepts eigene Betriebsdaten genutzt. Die Machbarkeit des neuen Verfahrens konnte das Konsortium in den Projekten «MACOR» und «BeWiSe» bereits nachweisen.
Demo-Anlage auf Werksgelände
Mit Blick auf die Ressourcen- und Energieeffizienz arbeiten die Forscherteams zusammen mit den Industriepartnern an der Optimierung der gesamten Prozesskette. Dazu wird auch eine rund 30 Meter hohe Direktreduktions-Demonstrationsanlage auf dem Werksgelände der Salzgitter AG genutzt. Beispielsweise wird im Rahmen des Projektes untersucht, wie biogene Stoffe als Ersatz für Kohle und Erdgas genutzt werden können, um den erforderlichen Kohlenstoffgehalt im Stahl einzustellen.
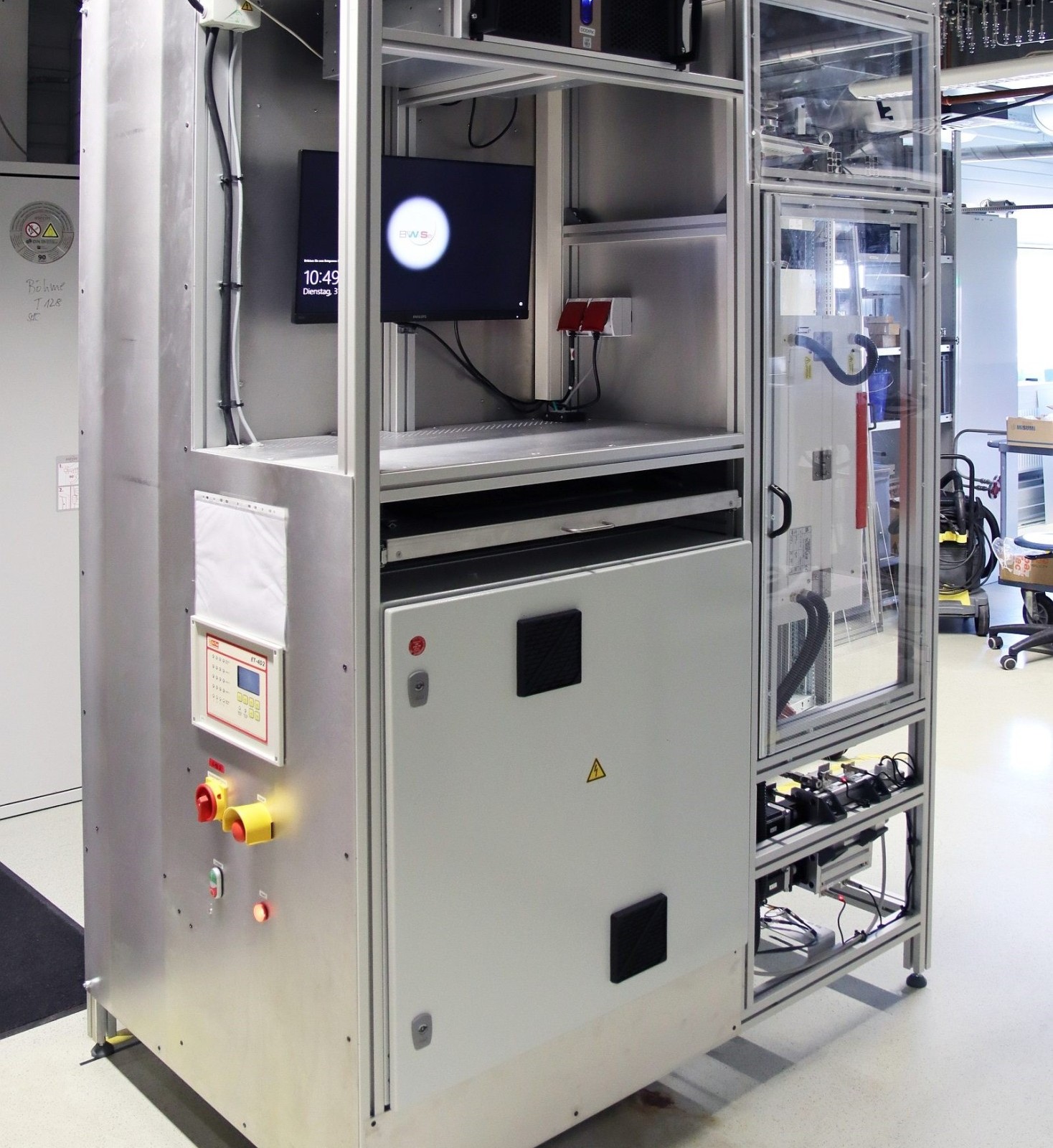
Quelle: Fraunhofer IKTS
Direktreduktionsanlage im Labormassstab für reaktionskinetische Untersuchungen und Modellierung des Schachtofens.
Zudem bildet der effiziente Einsatz von Wasser einen Schwerpunkt im Projekt, denn in der Produktion von grünem Stahl werden unter anderem für die Elektrolyse grosse Mengen an Wasser benötigt. Daher soll das bei der Eisenerz-Reduktion mit Wasserstoff gebildete Wasser möglichst für die erneute Nutzung aufbereitet werden. Gefördert wird das Vorhaben «BeWiSe» vom Bundesministerium für Bildung und Forschung (BMBF).
Ein Drittel der Produktion bis 2026
Um dem Verfahren bei der praktischen Anwendung zum Durchbruch zu verhelfen, ist eine breite Palette von Expertisen gefragt. Die Wissensgebiete umfassen laut den Forschungsinstituten von der Hochtemperatur-Elektrolyse über Membranverfahren zur Gastrennung und Wasseraufbereitung auch die Prozesssimulation und Modellierung der Anlagen mithilfe eines digitalen Zwillings. Ziel der intensivierten Forschungsaktivitäten sind nicht punktuelle Lösungen und Laboranlagen. Vielmehr bietet die Forschung laut Gregor Herz, dem Gruppenleiter Modellierung und Simulation am Fraunhofer IKTS, der Salzgitter AG eine umfassende technologische Begleitung bei allen Prozessschritten. Bei der Forschung und praktischen Umsetzung mit von der Partie ist auch die «TS Elino GmbH». Die Demonstrationsanlage zur Direktreduktion ermöglicht es, den Reduktionsprozess und das Zusammenspiel mit den weiteren technischen und ökonomischen Folgeschritten zu optimieren. Seit sechs Jahren arbeiten die Fraunhofer-Forscher gemeinsam mit dem Unternehmen an der Transformation der Stahlerzeugung. Bereits 2026 will die Salzgitter AG einen Drittel der Stahlproduktion auf das Verfahren mit Wasserstoff umstellen.
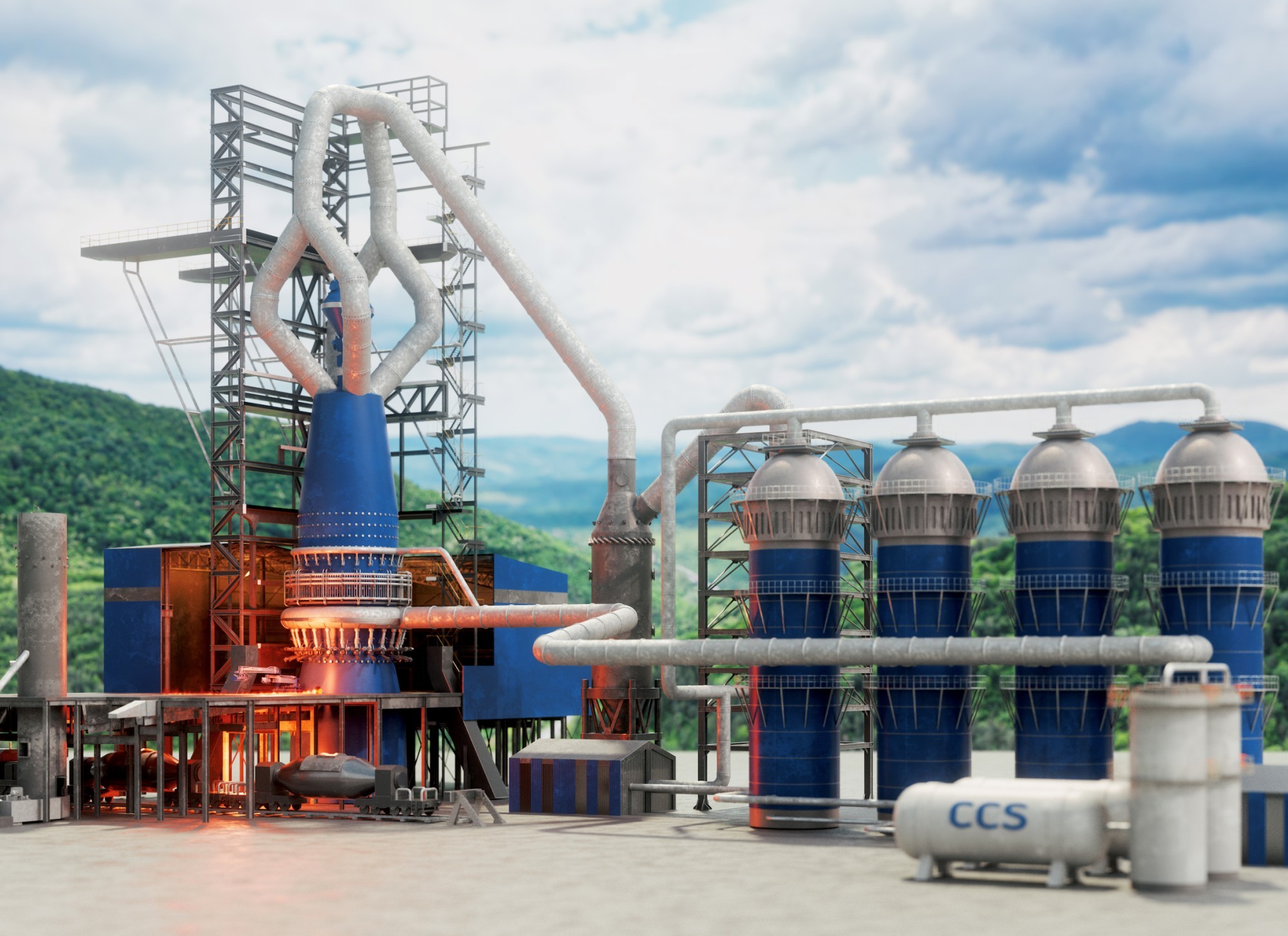
Quelle: SMS group
Durch die Integration von Hochofen und Kokerei sowie das konsequente Recycling von Prozessgasen und -wärme kann der CO2-Ausstoß bei der Stahlproduktion reduziert werden.
Bestehende Anlagen fit machen
Langfristig bietet die neue Wasserstofftechnologie eine klimaneutrale Perspektive. Doch bis dafür weltweit ausreichend grüner Wasserstoff zur Verfügung steht und neue Anlagen effektiv den Betrieb aufnehmen, werden noch Jahre vergehen. «In der Klimakrise haben wir dafür keine Zeit, wir müssen schon jetzt gegensteuern», mahnt Olaf Deutschmann, Professor am Institut für Technische Chemie und Polymerchemie (ITCP) des renommierten Karlsruher Instituts für Technologie (KTI). Schnell einen deutlichen Effekt auch in konventionellen Anlagen erzielen liesse sich mit einem neuen Verfahren, das eine Forschungsgruppe unter seiner Leitung gemeinsam mit den Industriepartnern «SMS Group», «Paul Wurth Entwicklungen» und der KIT-Ausgründung «Omegadot» demonstriert hat. Deutschmann schätzt, dass sich durch die Nachrüstung bestehender Hochöfen etwa zwei bis vier Prozent der weltweiten direkten Emissionen an Kohlendioxid einsparen lassen. Und dies bei moderaten Investitionskosten.
Zwölf Prozent weniger Emissionen
Mit dem neuen Verfahren wird Kohlendioxid aus dem Hochofengas mit Kokereigas rezykliert. Als Resultat entsteht ein Synthesegas mit hohem Wasserstoffanteil, das als Koksersatz im Hochofen genutzt werden kann, wie das KTI in einer Mitteilung schreibt. Das neue Verfahren setzt beim Rohstoff Eisen an, den die Stahlwerke meist direkt aus Bergbauerzen gewinnen, in denen er in oxidierter Form vorliegt.
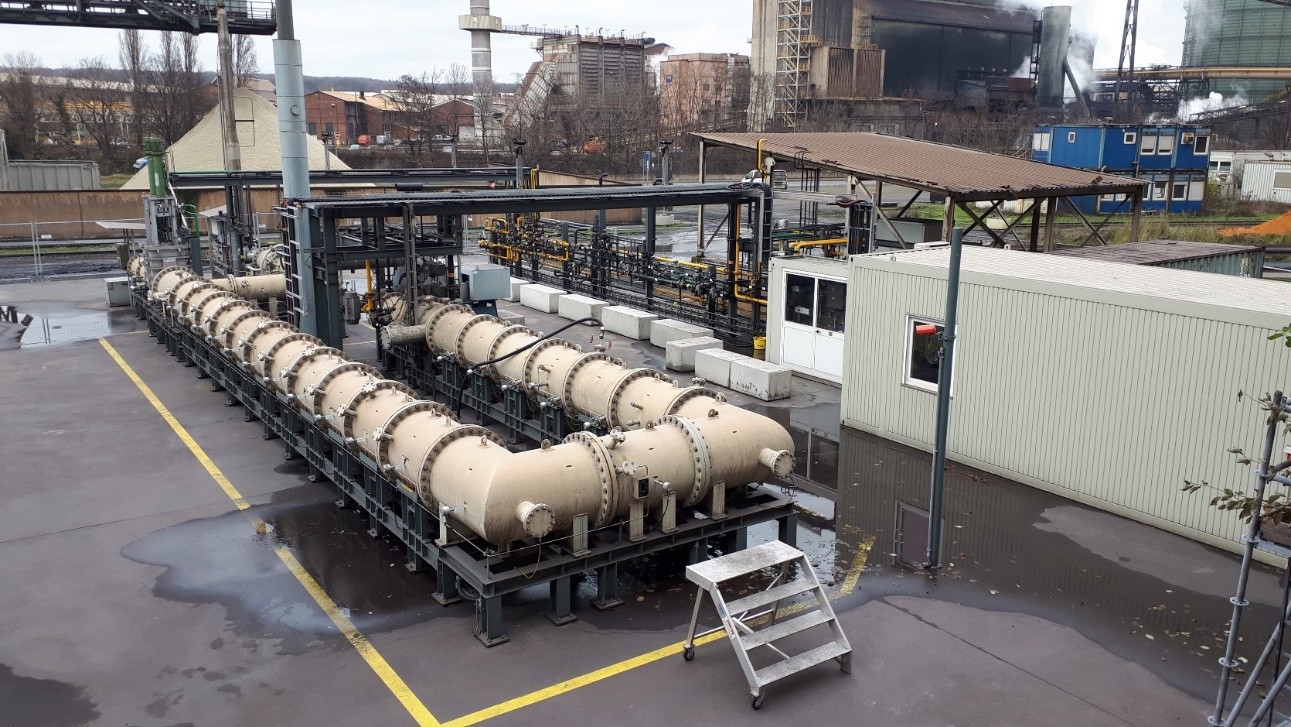
Quelle: SMS group
Pilotanlage im Saarland, mit der das neue Verfahren zur Eisengewinnung bereits demonstriert wird.
Um eine bestehende Anlage nachzu-rüsten, müssen vorhandene Heisswinderzeuger, auch Cowper genannt, modifiziert werden. In diesen Cowpern werden dann Methan und Kohlendioxid aus dem Kokereigas zusammen mit Kohlendioxid aus dem Hochofengas zu Synthesegas, bei dem es sich um ein Gemisch aus Wasserstoff und Kohlenmonoxid handelt. Dieser «Trockenreformierung» genannte Prozess erfordert eine hohe Temperatur, die zum grossen Teil aus der Prozesswärme des Hochofens gewonnen wird. Das Synthesegas wird anschliessend in den Hochofen eingeblasen, um dort die Reduktion des Eisenoxids zu unterstützen. «Pro Tonne erzeugtem Stahl können auf diese Weise signifikante Mengen an Koks eingespart werden, was wiederum die spezifischen CO2-Emissionen um bis zu zwölf Prozent senkt», sagt Philipp Blanck vom ITCP, der eng mit dem Unternehmen SMS Group an der im Stahlwerk integrierten Pilotanlage zusammengearbeitet hat.
Gewichtiger Schritt der Stahlindustrie
Simulationen und Visualisierungen des Verfahrens bilden die Grundlage für den Transfer der Erkenntnisse aus den Forschungen zum praktischen Einsatz des Verfahrens in einer Industrieanlage. Demonstrationen und Validierungen des Verfahrens erfolgten auf dem Areal der Dillinger Hüttenwerke im Saarland. Die Pilotanlage wird von der SMS-Group gemeinsam mit den Partnern Dillinger und Saarstahl betrieben. Erklärtes Ziel der Unternehmen ist es, Stahl mit weniger CO2-Emissionen zu produzieren. Für Gilles Kass, der bei der «SMS Group» die Forschungsaktivitäten begleitet, ist die Integration des neuen Verfahrens in das Werk in Dillingen ein erster Schritt der Stahlindustrie auf dem Weg der Transformation. (mgt/sts)
Stahlherstellung neu gedacht
Bei der Herstellung von Stahl muss der Sauerstoff aus den Eisenerzen herausgelöst werden. Dieser zentrale Produktionsschritt erfolgte bisher vor allem über den Hochofenprozess unter Verwendung von Koks, der für diese Zwecke in einem energieintensiven Prozess aus fossiler Kohle gewonnen werden muss und den Ausstoss grosser Mengen von Kohlendioxid zur Folge hat. Damit das Klimagas bei der Stahlproduktion reduziert werden kann oder gar nicht erst anfällt, gerät das Direktreduktionsverfahren vermehrt ins Blickfeld von Wissenschaft und Industrie. Die Reduktionsgase Kohlenmonoxid- und Wasserstoffgas werden bei Temperaturen von rund 1000 Grad Celsius in den Ofen geblasen, die dabei die Eisenerze durchströmen und den Sauerstoff herauslösen. Da die rissige Oberfläche einem porösen Schwamm ähnelt, wird das Zwischenprodukt auch Eisenschwamm genannt. Das desoxidierte und stark eisenhaltige Erz wird dann, allenfalls unter Beimischung von Recycling-Schrott oder Roheisen, meist mittels des Elektrostahlverfahrens (Lichtbogen-Verfahren) bei Prozesstemperaturen von über 3000 Grad Celsius zu Rohstahl verarbeitet. Denn Roheisen kann weder geschmiedet noch gewalzt werden. (mgt/sts)