Hochpräzise Metallbauteile aus dem 3D-Drucker mit Strom
Forscher der Universität des Saarlandes formen auf Tausendstel Millimeter genau komplizierte Bauteile aus hochbelastbaren Metallen. Das Team bedient sich hierfür einer Kombination aus 3D-Druck und elektrochemischem Abtragen.
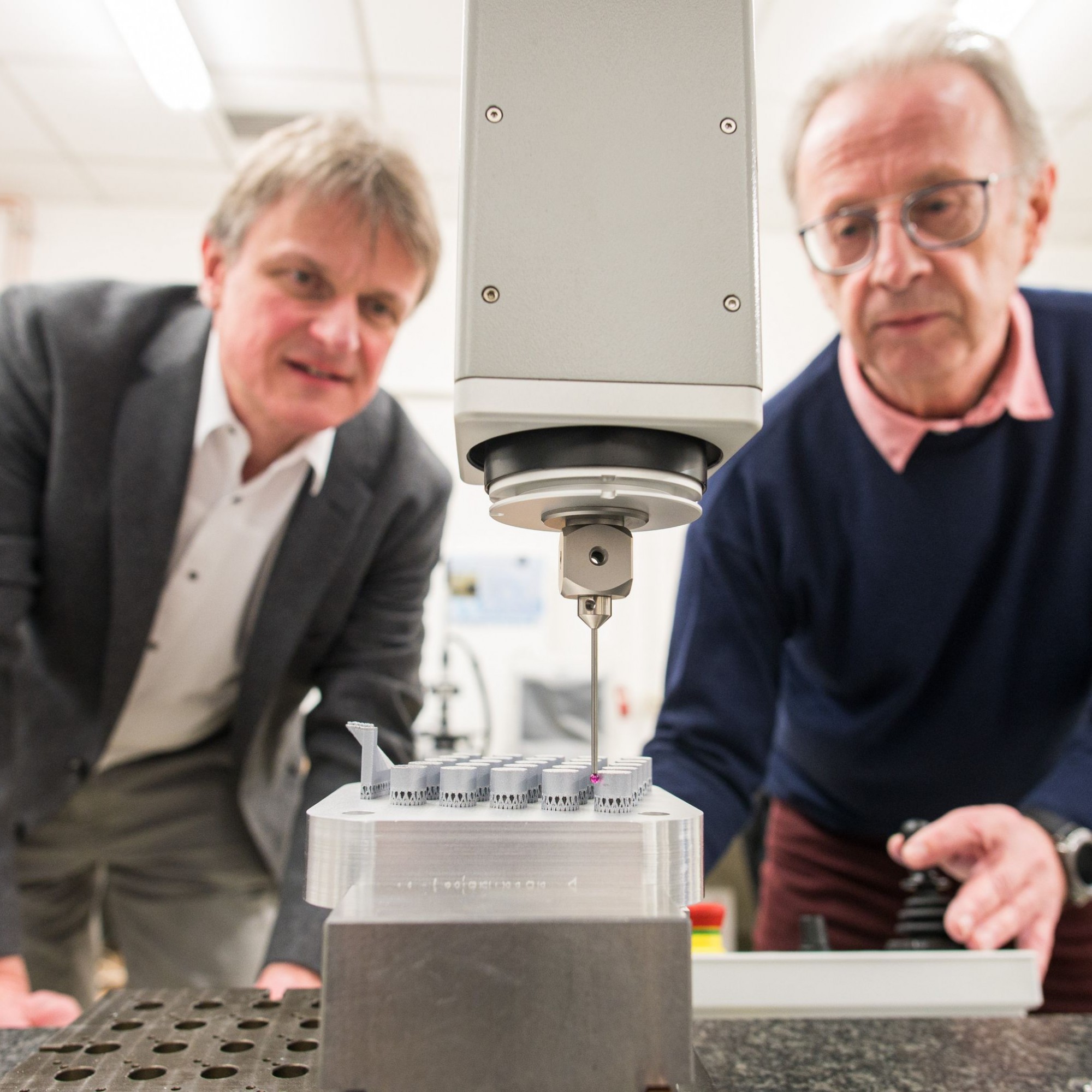
Quelle: © Oliver Dietze
Die Feinbearbeitung ist Spezialität der Saarbrücker Fertigungstechniker um Professor Dirk Bähre (l., hier mit dem technischen Mitarbeiter Stefan Wilhelm aus seiner Forschungsgruppe).
Technische Konstruktionen wie Fahrzeugmotoren, Flugzeug-Triebwerke oder Raketen bestehen aus einer Vielzahl spezieller Metallbauteile. Jedes Einzelteil muss dabei perfekt geformt sein, damit die Elemente später zu 100 Prozent zusammen- und ineinanderpassen und dadurch den härtesten Bedingungen standhalten können.
Die Toleranzen liegen hierbei im Mirkometerbereich, wie Professor Dirk Bähre in einer Medienmitteilung der Universität erklärt. Zwar ermöglichten 3D-Druckverfahren heute bereits die Herstellung komplizierter Bauteile. Jedoch würden die Resultate aus der sogenannten additiven Fertigung oft nicht für hohe Ansprüche ausreichen. Das Verfahren stosse bei manchen Geometrien schlicht an seine Grenzen.
Veredelung von 3D-Druck-Werken
Dirk Bähre und sein Team forschen deshalb daran, Werkstücke aus dem 3D-Drucker so zu veredeln, dass sie auf den Tausendstel Millimeter genau passen. «Mit unseren Technologien zur Nachbearbeitung additiv gefertigter Metallteile können wir Präzisionsfunktionsflächen für hochgenaue Anwendungen kostengünstig herstellen», erklärt Bähre in der Mitteilung. Auch hohe Stückzahlen könnten dadurch wirtschaftlich produziert werden.
Die Feinbearbeitung gehört zur Spezialität der Forschungsgruppe. Das Team konnte bereits neuartige Verfahren entwickeln, die auf einer Kombination aus metallischem 3D-Druck und elektrochemischem Abtragen basieren. Durch letzteres lassen sich selbst komplizierteste Geometrien in härtestem Metall umsetzen. Dabei handelt es sich um eine schädigungsfreie, berührungslose Fertigungstechnologie, mit der sich komplexe Bauteile und hochfeste Werkstoffe effizient bearbeiten lassen.
Elektrischer Strom formt Bauteile
Umspült von einer Elektrolytlösung, nehmen die Werkstoffe bis auf den Tausendstel Millimeter genau die gewünschte Geometrie an. Ohne Kraftaufwand oder mechanische Einwirkungen. Benötigt wird dafür lediglich elektrischer Strom: Dieser fliesst zwischen einer als Vorlage dienenden Kathode und einer Anode – die in diesem Fall den zu bearbeitenden Werkstoff darstellt – aus dem 3D-Drucker.
Umspült von einer stromleitenden Flüssigkeit aus Wasser und Salz werden dabei winzige Metallteilchen abgetragen: Die Metallionen lösen sich und das hochpräzise Bauteil entsteht. Stromimpulse und Schwingungen des Werkzeuges ermöglichen laut Bähre zudem einen besonders gleichmässigen Abtrag mit sehr glatten Oberflächen und hoher Genauigkeit.
Verständnis von Werkstoff und Verfahren
Um die Nachbearbeitung zu optimieren sei ein tiefes Verständnis von Werkstoff und Verfahren nötig. Die Forscher nehmen deshalb die zum Einsatz kommenden Metalle wie Aluminium, Titan oder auch Stahllegierungen genau unter die Lupe und verfolgen jeden Prozessschritt. «Wir müssen genau verstehen, was beim 3D-Druck mit dem Metall passiert.», wie Bähre erklärt. «Daher ergründen wir, welche Gefügestruktur dabei entsteht.» Mit der Erforschung von Verfahren und Materialverhalten lassen sich die elektrochemischen Methoden weiterentwickeln.
Im Rahmen dessen stellen dieForscher derzeit in einer Vielzahl von Experimenten Teile im 3D-Drucker her und ergründen, wie die jeweils passende elektrochemische Bearbeitung erfolgen muss. Dabei werden alle Einflüsse systematisch unterteilt sowie hochgenaue Messungen vorgenommen und Detailanalysen erstellt. Dadurch würden sich laut Mitteilung viele Stellschrauben ergeben, mit denen die Verfahren massgeschneidert und die Prozesseinstellungen gezielt angepasst werden können. (mgt/pb)
Weitere Informationen: https://www.uni-saarland.de/universitaet/aktuell/artikel/nr/21918.html