Erdsondenbohrung in Zermatt: Mit Hochdruck und Feingefühl
Mitten im Touristenort Zermatt werden für die Erdsonden-Heizung in einem neuen Schulhaus 40 Bohrungen von 140 Meter Tiefe erstellt. In anderen Regionen der Schweiz ist dies ein Routinejob, doch am Fusse des Matterhorns braucht es einen erfahrenen Bohrmeister, um die teure Ausrüstung durch die komplexe Geologie zu manövrieren.
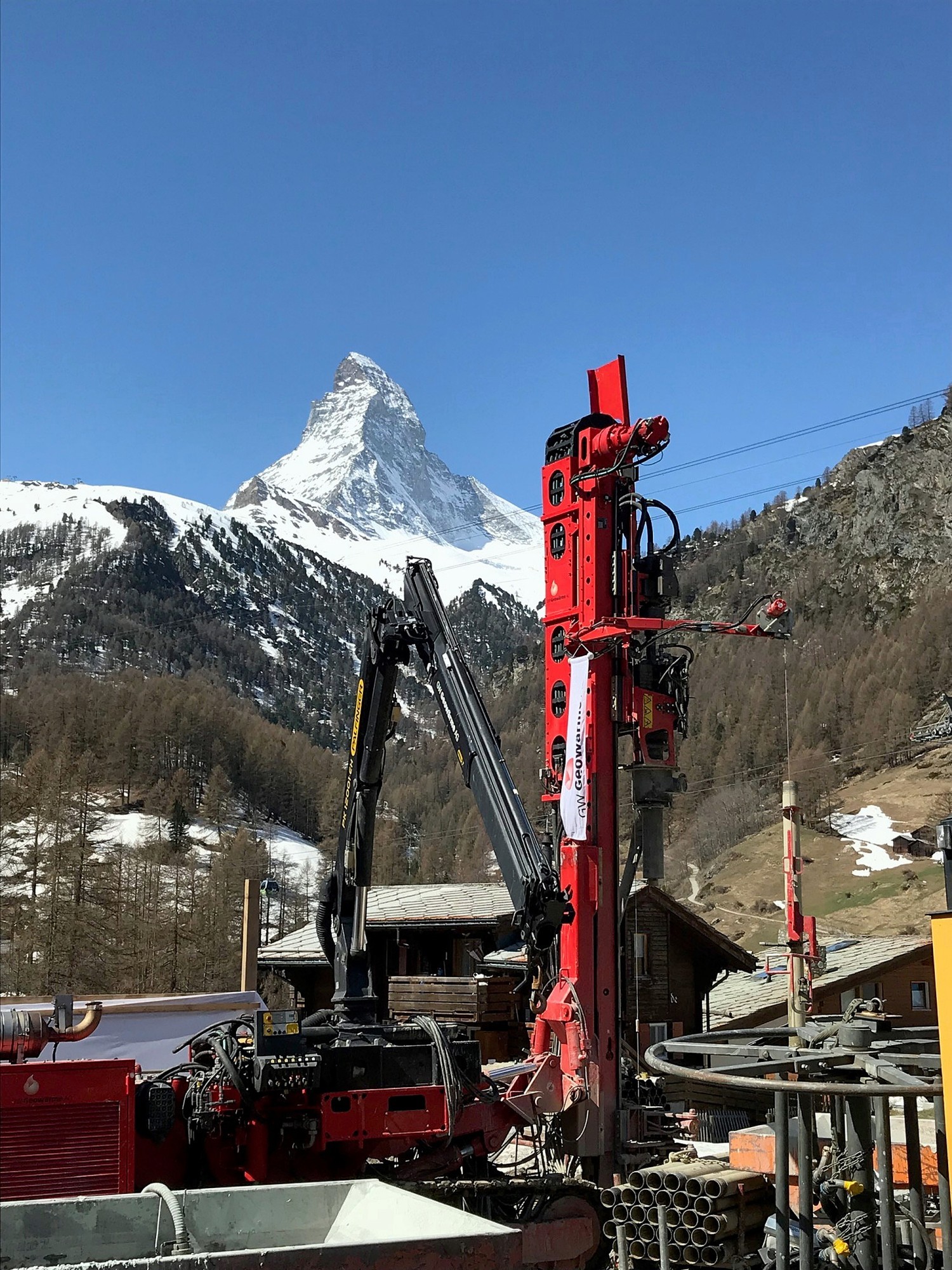
Quelle: Philipp Schmid / Geowärme AG
Erdsondenbohrung vor Postkartenkulisse.
Beim Kirchplatz im Zentrum Zermatts tummeln
sich die Touristen und suchen die beste Perspektive fürs obligate Selfie. Nur
50 Meter weiter hangaufwärts, weitgehend abgeschirmt durch die dichte Bebauung,
werden im Akkord Löcher ins Erdreich abgetäuft.
Bohrmeister Savo Dragojlovic von der
Geowärme AG und sein Hilfsbohrmeister Bozo Tadic arbeiten unter ständigem
Druck: Sie müssen innert kurzer Zeit zwölf Bohrlöcher von 140 Meter Tiefe
erstellen, und sich dabei exakt an den vorgegebenen Zeitplan halten. Denn auf
der Baustelle zum neuen Zermatter Schulhaus Niww-Walka ist der Platz so knapp
wie überall im Dorfkern. Für 45 Millionen Franken errichtet hier die Walliser
Gemeinde einen Ersatzneubau mit 22 Klassenzimmer, Eventbühne, Turnhalle und
Mensa.
Das Klemm-Bohrgerät samt zusätzlicher
Ausrüstung muss deshalb ständig den Standort wechseln, nach einem mit dem
Baumeister detailliert ausgearbeiteten Plan, damit man die anderen Bauarbeiten
nicht behindert. Doch Dragojlovic und sein Assistent sind ein erfahrenes Team
und gut im Soll. «Wir müssen mit viel Gefühl vorgehen», erklärt der
Bohrmeister.
«Anderenorts kann man im Sandstein 50 Meter
in der Stunde bohren. Hier im Oberwallis ist die Geologie ganz anders, der
Untergrund bald felsig. Ich bohre deshalb maximal zehn Meter pro Stunde.»
Sowohl die Bohrwerkzeuge als auch die dazu passenden Leistungsparameter des
Bohrgerätes, wie Vorschub, Drehzahl und Drehmoment, werden auf solche
Situationen angepasst
Nichts für «On-Off-Maschinisten»
Renato Genasci, Verkaufsberater Bautechnik
Avesco AG, bestätigt: «Man darf diese Aufgabe nicht unterschätzen: Der
Maschinist macht mehr als 50 Prozent aus. Er spürt und hört sozusagen die
anstehende Geologie, also die Bodenschichtung, und steuert die Maschine
entsprechend vorsichtig.» Es gebe auch «On-Off-Maschinisten, die immer auf
Tutti gehen». Aber bei denen geht viel rascher ein Gewinde kaputt, der Bohrkopf
verschleisst oder das Gestänge nimmt Schaden. «Ein guter Bohrmeister kann
seinem Unternehmen viel Geld sparen und verdienen.»
Der Unternehmer ist in diesem Fall die Walliser Spezialfirma Geowärme AG. Geschäftsführer Philipp Schmid erklärt das Besondere an diesem Projekt: «Wir haben im Kanton viele Bauvorhaben mit nur ein oder zwei Bohrungen. Hier sind es 40, was es zu einem Grossprojekt macht.» Neben der Dimension ist auch der Strassentransport der gesamten Ausrüstung nach Zermatt sehr anspruchsvoll. «Wir haben sehr grosse Maschinen und benötigen Sonderbewilligungen sowie Polizeibegleitung.»
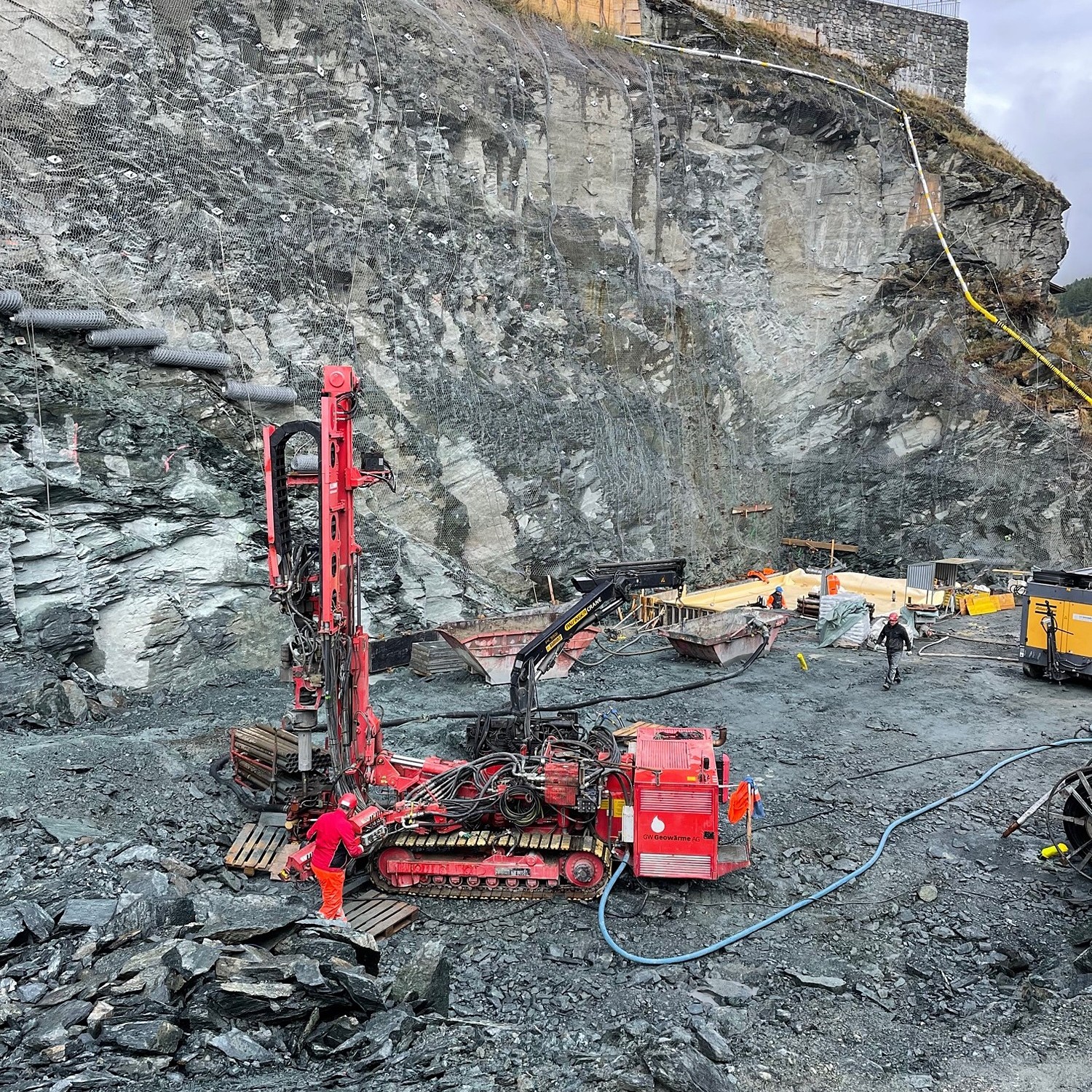
Quelle: Philipp Schmid / Geowärme AG
Erste Probebohrung 2021: An der Felswand lässt sich erahnen, wie komplex die Erdschichten im Untergrund angeordnet sind.
Bohrungen in Etappen
Die erwähnten Platzverhältnisse seien eine weitere Herausforderung. «Wir mussten bereits 2021 die ersten 21 Bohrungen vornehmen, da diese unterhalb der neuen Bodenplatte liegen.» Jetzt steht der Rohbau des neuen Schulhauses, und auf dem schmalen Landstreifen daneben folgen die nächsten 12 Bohrungen. Die letzten 6 erfolgen nächstes Jahr, nach dem Rückbau des dritten der alten Schulhäuser. Bei dieser Addition fehlt natürlich noch die allerersten Testbohrung zu Baubeginn.
Der Umzug der Bohrmaschine ist dabei keine Kleinigkeit: Zur Ausstattung des mächtigen Gerätes gehört ein fast ebenso grosser Kompressor, daneben braucht es Platz für die Bohrgestänge und weitere Ausrüstungen. Und dann müssen noch sechs Mulden Platz finden: In ihnen wird der so genannte Bohrrückfluss erst gesammelt und dann stehengelassen, bis sich genügend Schwebstoffe abgesetzt haben. Das nun schon etwas klarere Wasser wird anschliessend zur Aufbereitung weitergeleitet, bis es alle Grenzwerte einhält und abgelassen werden kann.
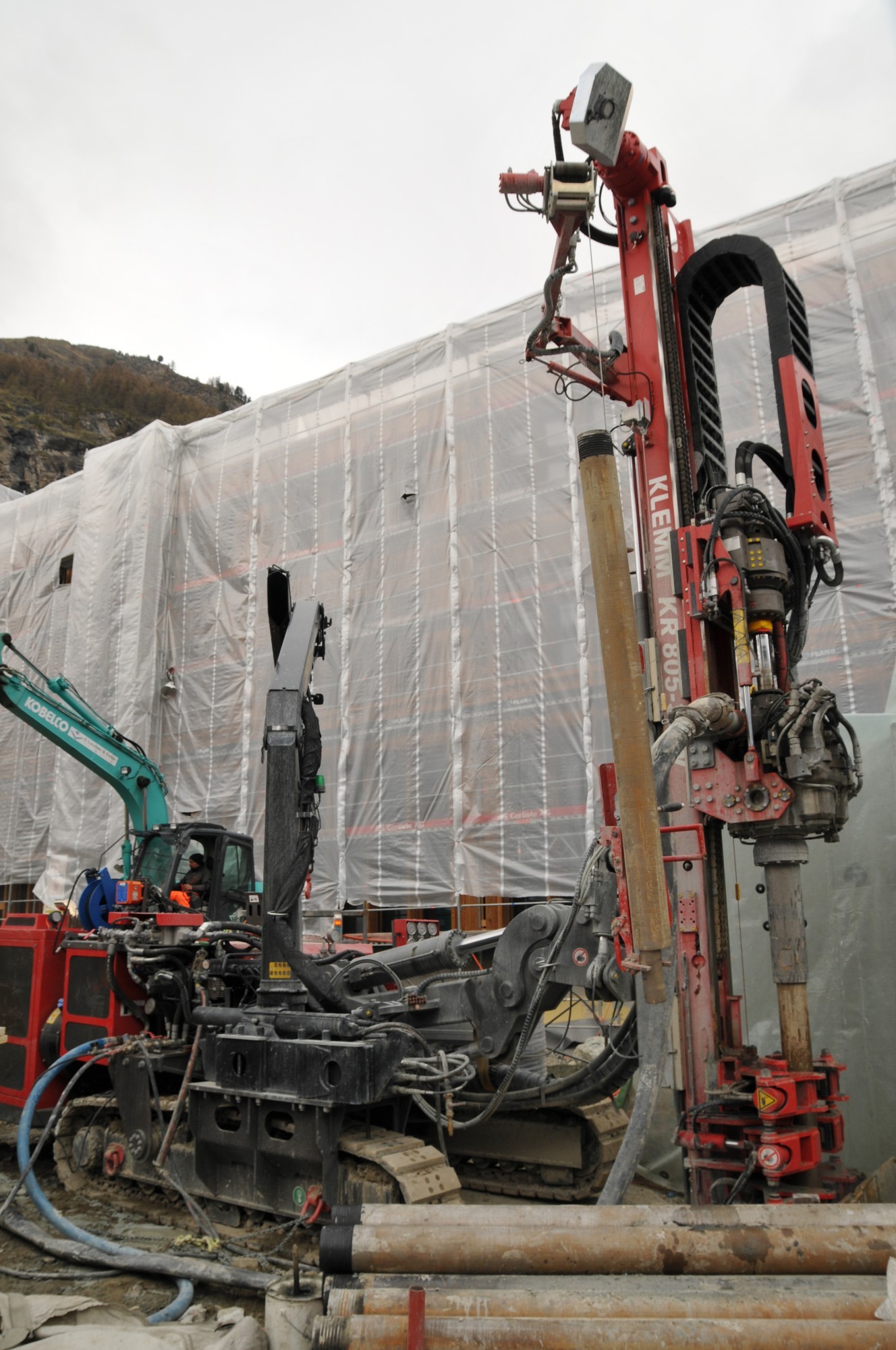
Quelle: Ben Kron
Das Erdsonden-Bohrgerät in voller Pracht: Auch Windlasten auf die Bohrlafette werden für die Standsicherheit berücksichtigt.
Beschränkte Bohrzeit
Der Zeitplan wird auch von der Umgebung diktiert: Aus Rücksicht auf die Tourismussaison darf nur im Frühjahr und Herbst während je vier Wochen gebohrt werden; wegen der Lärmentwicklung und weiterer Emissionen. Mit Gesuchen lässt sich die Bohrzeit jeweils auf acht Wochen verlängern, aber mehr nicht. Auch das Klima schränkt das Bohrbusiness ein: Bei Minusgraden gefriert das zur Bohrung benötigte Wasser; je nach Witterung ist zwischen Dezember und März zumindest in höheren Lagen Bohrpause, da ein wirtschaftliches Arbeiten so nicht möglich ist. Dann arbeitet Dragojlovic bei einem Partnerunternehmen, während sein Kollege als Skilehrer den Winter verbringt.
”«Tiefer als 140 Meter war nicht möglich, da wir hier am Fusse des Matterhorns schwierige geologische Verhältnisse haben.»
Philipp Schmid, Geowärme AG
Philipp Schmid, Geowärme AG
Diese Gesamtzahl von 40 Bohrungen ergibt sich aufgrund der vorab gemachten Untersuchungen. Mit der erwähnten Probebohrung wurde zuerst ermittelt, wie tief sich die Erdsonden abteufen lassen. Schmid: «Tiefer als 140 Meter war nicht möglich, da wir hier schwierige geologische Verhältnisse haben: Mal stossen wir auf Quarz, mal auf Granit, eine Schicht eines Felssturzes, Schiefer, lockeres Moränenmaterial.»
Das Problem: Bei sehr wechselndem, teilweise geschichtetem Untergrund lassen sich mit einem starken Bohrgerät zwar gut auch tiefe Löcher bohren, aber gleichzeitig gibt es in solchen Verhältnissen ein erhöhtes Risiko für Hohlräume im Boden. Beim Zurückziehen des Bohrgestänges kann Lockermaterial nachrücken und das Bohrloch verstopfen. In diesem Fall lässt sich anschliessend die Erdsonde nur noch bis zu dieser Verstopfung abteufen. Der Rest der Bohrung war dann quasi vergeblich.
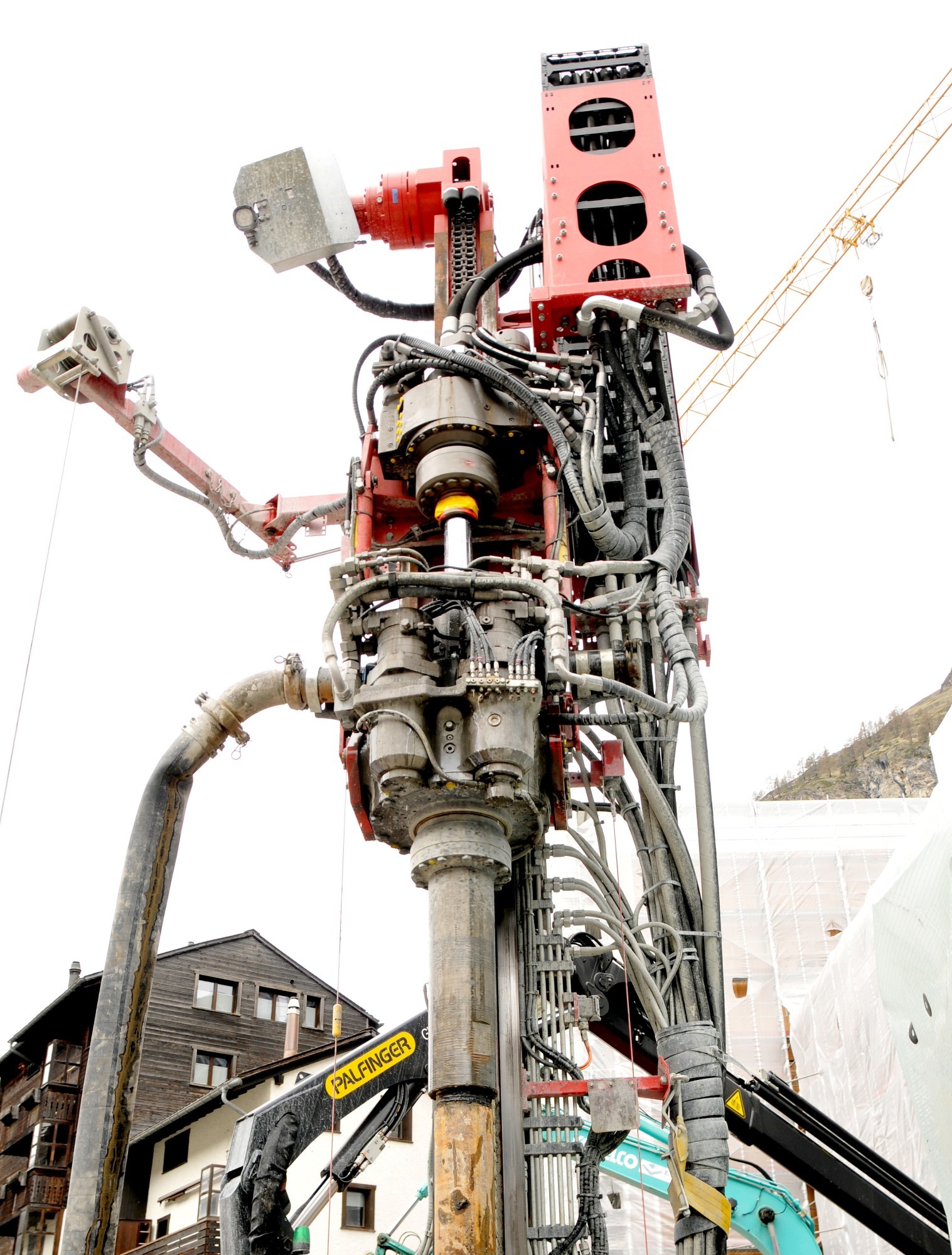
Quelle: Ben Kron
Ein ausgeklügeltes System sorgt dafür, dass die Kraft zwischen den einzelnen Antrieben stets optimal verteilt ist.
Überall Risse und Klüfte im Fels
«In der Deutschschweiz kennt man das nicht», so Schmid. «Hier bohrst Du 300 Meter in einem Fels wie in Beton, sauber, trocken, kompakt und homogen. Wir im Wallis haben überall Risse und Klüfte in den Felsen.» Ein Blick auf die Felswand nach dem Aushub der Baugrube illustriert diese schwierigen geologischen Verhältnisse.
Zu den Probebohrungen gehört ein so genannter Thermal Response Test: Nach einer Bohrung wird für eine Woche der Betrieb einer Erdsonde simuliert und dabei ermittelt, wie viel Wärme sich auf Dauer im Erdreich speichern und dann wieder entziehen lässt. Aus dem Test ergab sich, dass man total 5600 Meter an Erdsonden benötigt Den Rest erledigt eine simple Bruchrechnung.
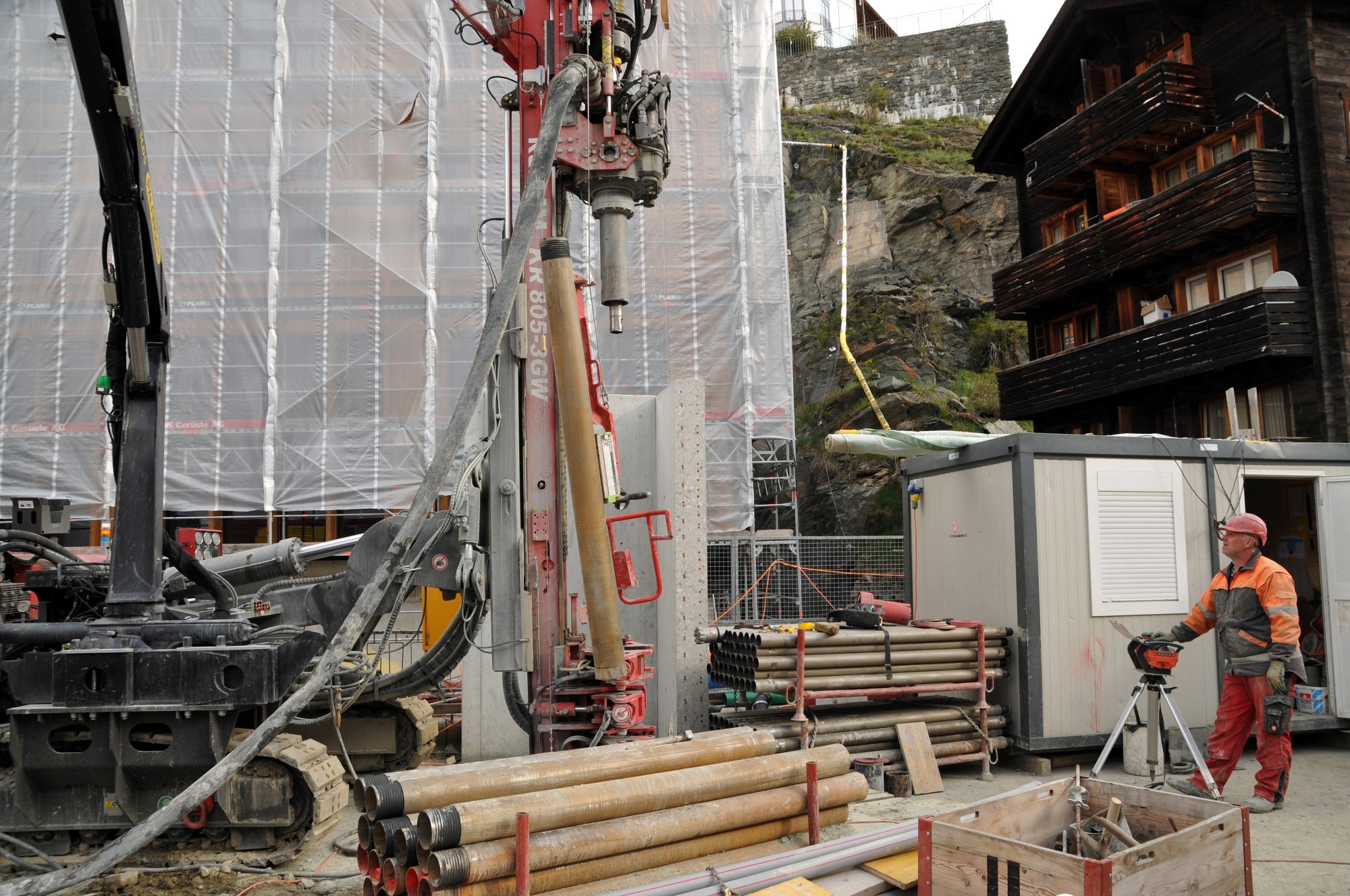
Quelle: Ben Kron
Savo Dragojlovic steuert das Gerät per Fernbedienung und hat seine Bohrung so stets gut im Blick.
Erst aussen, dann innen
Die Bohrungen erfolgen jeweils in Abfolge mehrerer Arbeitsschritte: Zuerst wird ein Mantelrohr samt Innengestänge in den Boden getrieben, bis dieses auf standfesten Fels stösst. Das Mantelrohr stabilisiert dabei das Bohrloch zum Erdreich. Von da an wird nur noch mit dem inneren Gestänge weiter gebohrt, an dessen Ende ein auf die Geologie angepasster Bohrkopf sitzt.
Ist die Bohrung «auf ihrer Zieltiefe» angelangt, wird zuerst das Innengestänge ausgebaut und danach die Erdsonde eingeführt. Das Mantelrohr stützt in diesem Schritt weiterhin das lockere, nicht standfeste Erdreich. Der hier 140 Meter lange Bohrstrang besteht aus vielen einzelnen, zwei Meter langen Teilstücken, den sogenannten Rohren und Gestängen. Beide sind an ihren Enden jeweils mit einem Vater- und einem Muttergewinde ausgestattet, wodurch sie sich kraftschlüssig verschrauben lassen.
Gründe für die Teilung in Zwei-Meter-Stücke liegen auch im Handling auf der Baustelle und der Lagerung auf dem Transportfahrzeug. Die Lafette des Bohrgerätes ist so ausgelegt, dass sie jeweils zwei Doppelrohre aufnehmen kann. «Natürlich hätten wir am liebsten einen Riesenturm für lange Bohrgestänge, um noch schneller arbeiten zu können», so Andreas Kumli, bei Avesco Verkaufsleiter Spezialtiefbau.
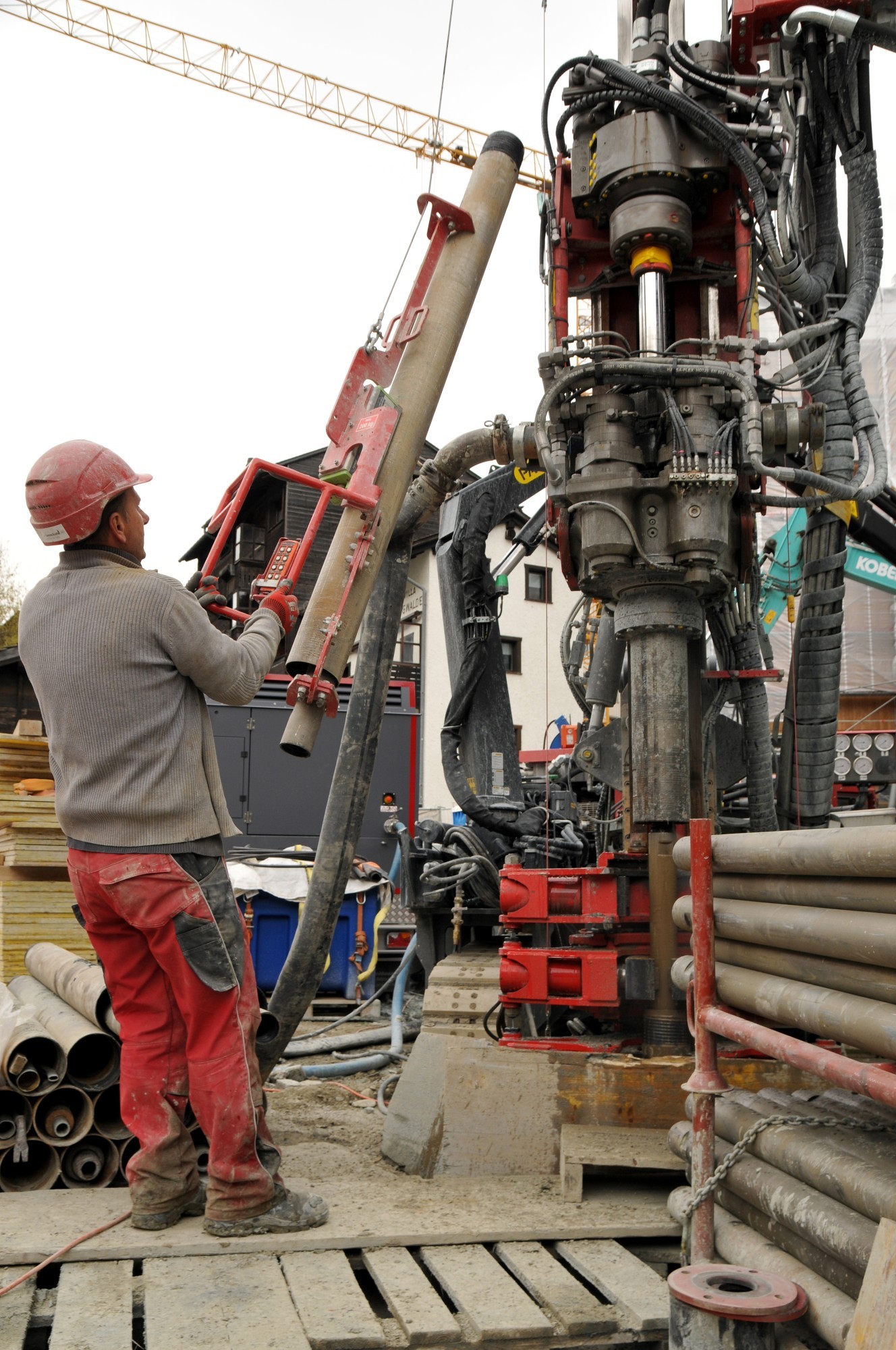
Quelle: Ben Kron
Ein integrierter Kran unterstützt Hilfsbohrmeister Bozo Tadic dabei, schwere Ausrüstungsteile an ihren Einsatzort zu heben.
«Aber das ist in der Baupraxis durch die Platzverhältnisse und auch physikalisch nicht möglich. Die Standsicherheit der Maschine muss zu jedem Zeitpunkt gewährleistet sein. Während der Entwicklung eines Bohrgerätes werden die Maschinenkonfiguration sowie sämtliche auf das Gerät wirkenden Kräfte erfasst. Ergebnis dieser Berechnungen sind die für den Betrieb zulässigen Bohrstellungen und Geländeneigungen. Sogar Windlasten auf die Bohrlafette sind ein Teil der nach den Normen zu berücksichtigenden Lasten.»
”«Das Bohrgerät ist vollgepackt mit elektronischen Hilfsmitteln, die den Kraftstoffverbrauch senken und die Performance optimieren.»
Beat Kumli, Avesco Verkaufsleiter Spezialtiefbau
Beat Kumli, Avesco Verkaufsleiter Spezialtiefbau
Kraft optimal verteilt
Beim eingesetzten Bohrgerät handelt es sich um das Modell KR 805-3GW von Klemm, einem der führenden Hersteller, der in der Schweiz von der Avesco vertrieben wird. Kumli bezeichnet es als «Rolls Royce» unter den Erdsondenbohrern. Das erst im Dezember 2022 in Betrieb genommene Gerät ist leistungsfähig, arbeitet sehr ruhig, dabei zuverlässig und sparsam. Natürlich erfüllt es die Euro-5-Abgasnormen. «Es ist vollgepackt mit elektronischen Hilfsmitteln, die den Kraftstoffverbrauch senken und die Performance optimieren.»
Die Bohrmaschine passt die Motordrehzahl an die benötigte Leistung an, was neben dem Kraftstoffverbrauch auch die Geräuschentwicklung immens senken kann. Das patentierte «Power Sharing», welches für die Hauptpumpen der Gerätehydraulik installiert ist, sorgt in den sich sehr häufig wechselnden Lastsituationen fortwährend und vollautomatisch für eine optimale Aufteilung der Hydraulikleistung auf die verschiedenen Hauptverbraucher, wie Drehen-Innen, Drehen-Aussen, Schnellvorschub und weitere.
«Das Gerät besitzt auch einen Kran, um das Zufuhrmaterial zu handeln», so Kumli weiter. Zusätzlich hat es Pumpen für Wasser und diverse Spülungsarmaturen zur Regelung von Druckluft- und Wasserspülung. «Besondere Merkmale des Gerätes sind sein Pendelfahrwerk und die flexible Mastkinematik: Die Kinematik ermöglicht es dem Bohrmeister, immer mit exakt derselben Neigung zu bohren und den Bohransatzpunkt in engen Platzverhältnissen bis an die Aussenkanten der Fahrspur zu versetzen, ohne das Bohrgerät mit drehen zu müssen. Mit dem Pendelfahrwerk passen sich die Raupenketten automatisch an jede Unebenheit des Bohrplatzes an.»
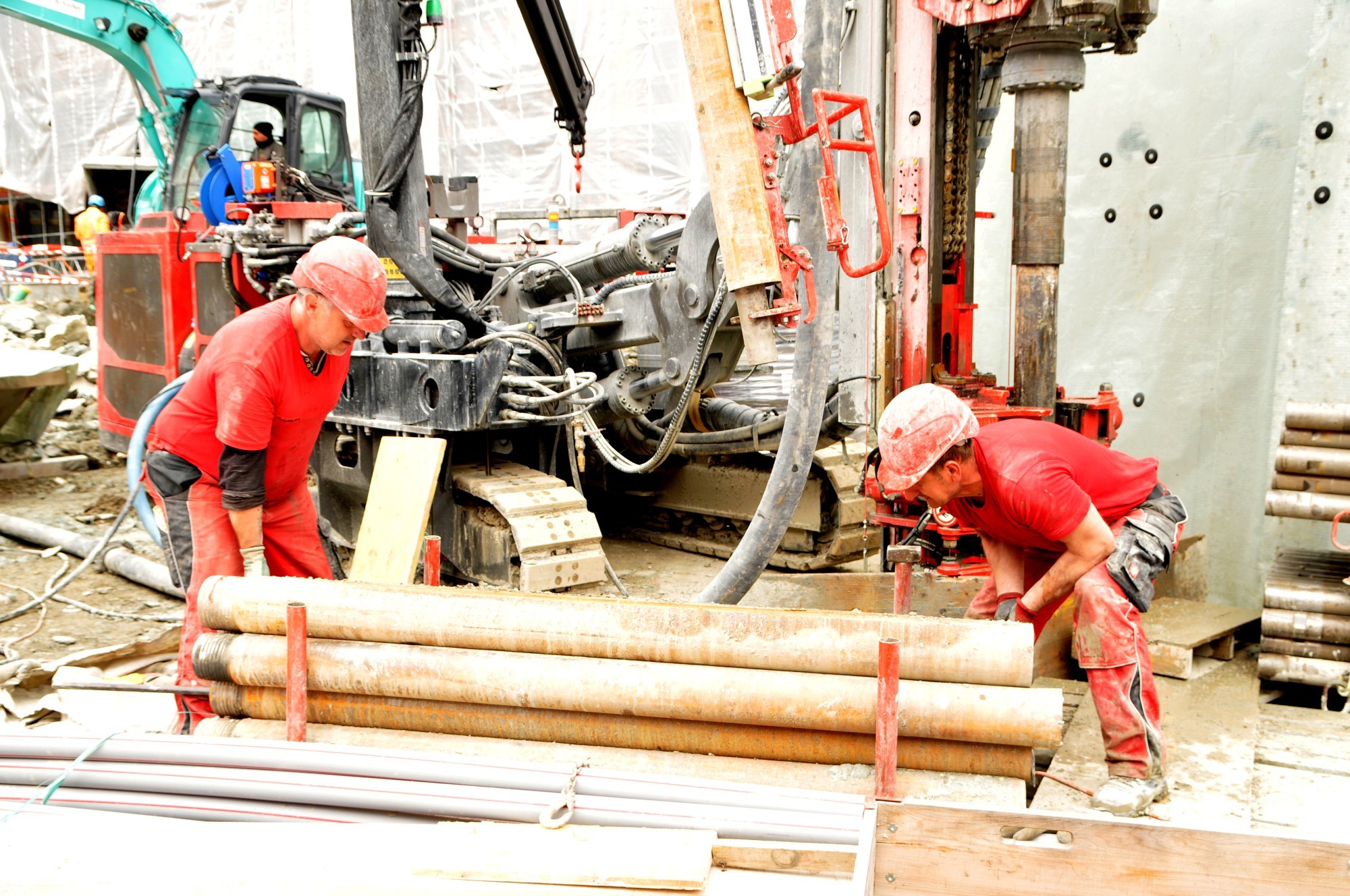
Quelle: Ben Kron
Gutes Teamwork zwischen den Bohrmeister und seinem Assistenten ist unerlässlich.
Schmuckstück Funkfernbedienung
Das Schmuckstück des 805-3GW ist die Funkfernsteuerung, wie Verkaufsberater Renato Genasci ausführt: «Wir haben auch bei der Fernbedienung einen Rolls Royce: Auf dem Gerät hat der Bohrmeister alle Informationen über seine Maschinen, also die Drehzahl beider Bohrantriebe, die Bohrtiefe, den Spülungsdruck und viele weitere Parameter.»
Der Bohrmeister hat weiter den Vorteil, dass er sich dort hinstellen kann, wo er die beste Sicht auf die Bohrung hat. «Die ersten Maschinen hatten die Steuerung nur an einem Pult an der Seite, so dass er gar keine Sicht auf die Bohrung hatte.» Die zweite Generation verfügte über eine Fernbedienung via Kabel. Die aktuelle Funkfernsteuerung kann sich der Bohrmeister umhängen oder von einem Dreibein aus bedienen.
Wenn ein technisches Problem auftaucht, schlägt die Maschine via Fernbedienung Alarm. Genasci: «Anhand der Art des Alarms können wir dann manchmal schon vom Telefon aus bei der Lösung des Problems helfen, ohne dass ein Monteur zum Einsatzort fahren muss. Das spart uns und auch der Bohrfirma Zeit und Geld.»
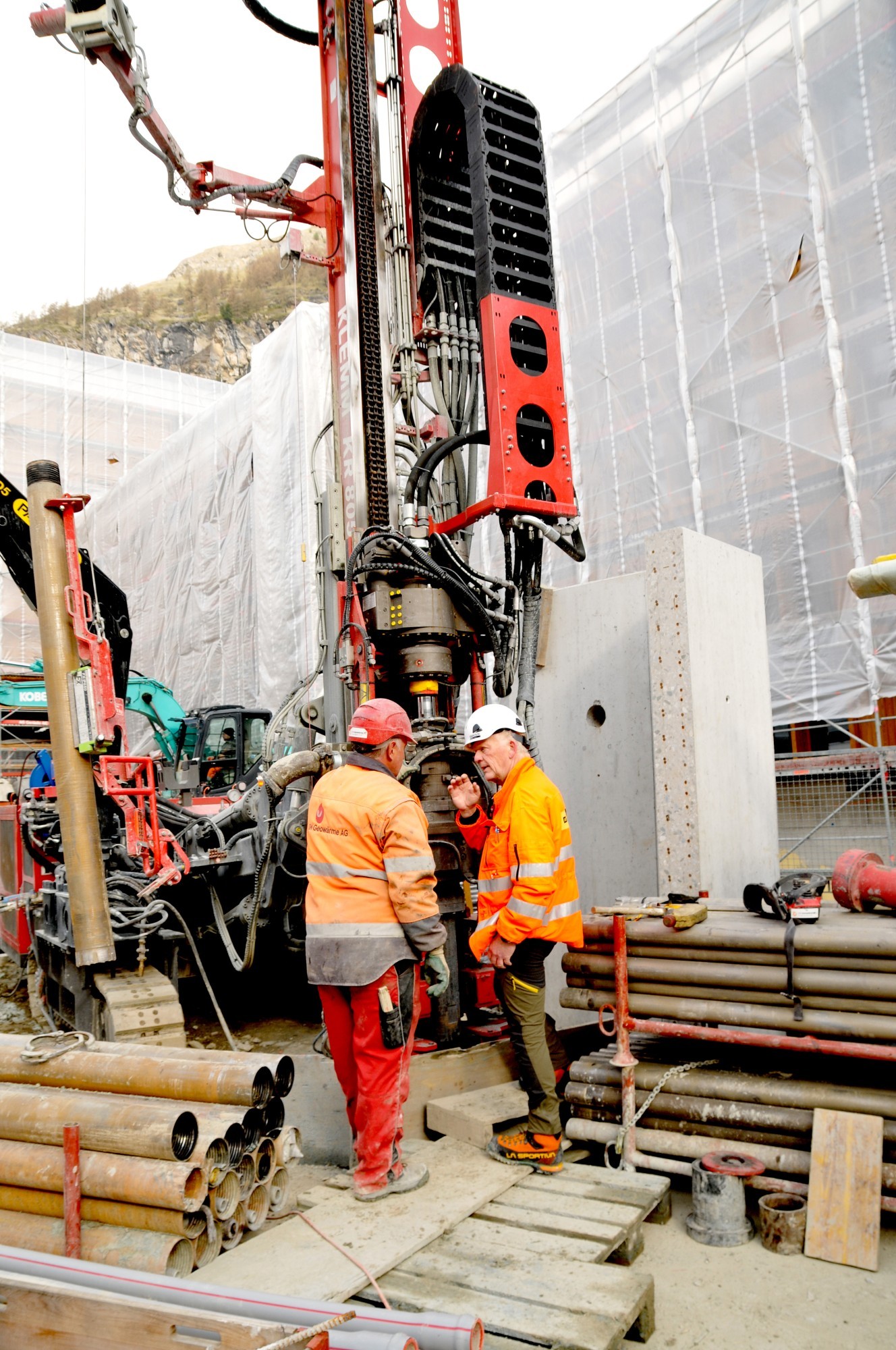
Quelle: Ben Kron
Bohrmeister Dragojlovic fachsimpelt mit Avesco-Verkaufsberater Renato Genasci (rechts).
Nach Gefühl und Gehör
Aktuell arbeitet Bohrmeister Dragojlovic mit einem Druck von 26 bis 27 Bar, was recht wenig ist. «Wir haben gerade feines Material, da bohre ich mit dem Mantelrohr langsam. Sobald das Mantelrohr wieder beim harten Material ansteht, bohre ich mit dem Innenrohr etwas schneller weiter. Aber auch hier nach Gefühl und Gehör, denn wenn im am falschen Ort pressiere, mache ich nur den Bohrkopf kaputt.»
Unvorsichtiges Bohren kann anschliessend auch Probleme machen, wenn man das Gestänge wieder herausziehen muss. Diese Arbeit ist schon wegen des Gewichts des zusammengesetzten Materials eine Herausforderung. Andreas Kumli: «Wenn wir dann das Gestänge nicht mehr herausbekommen, ist die Bohrung sozusagen verloren und das Unternehmen hat viel Geld im wahrsten Sinne des Wortes 'verlocht'.»
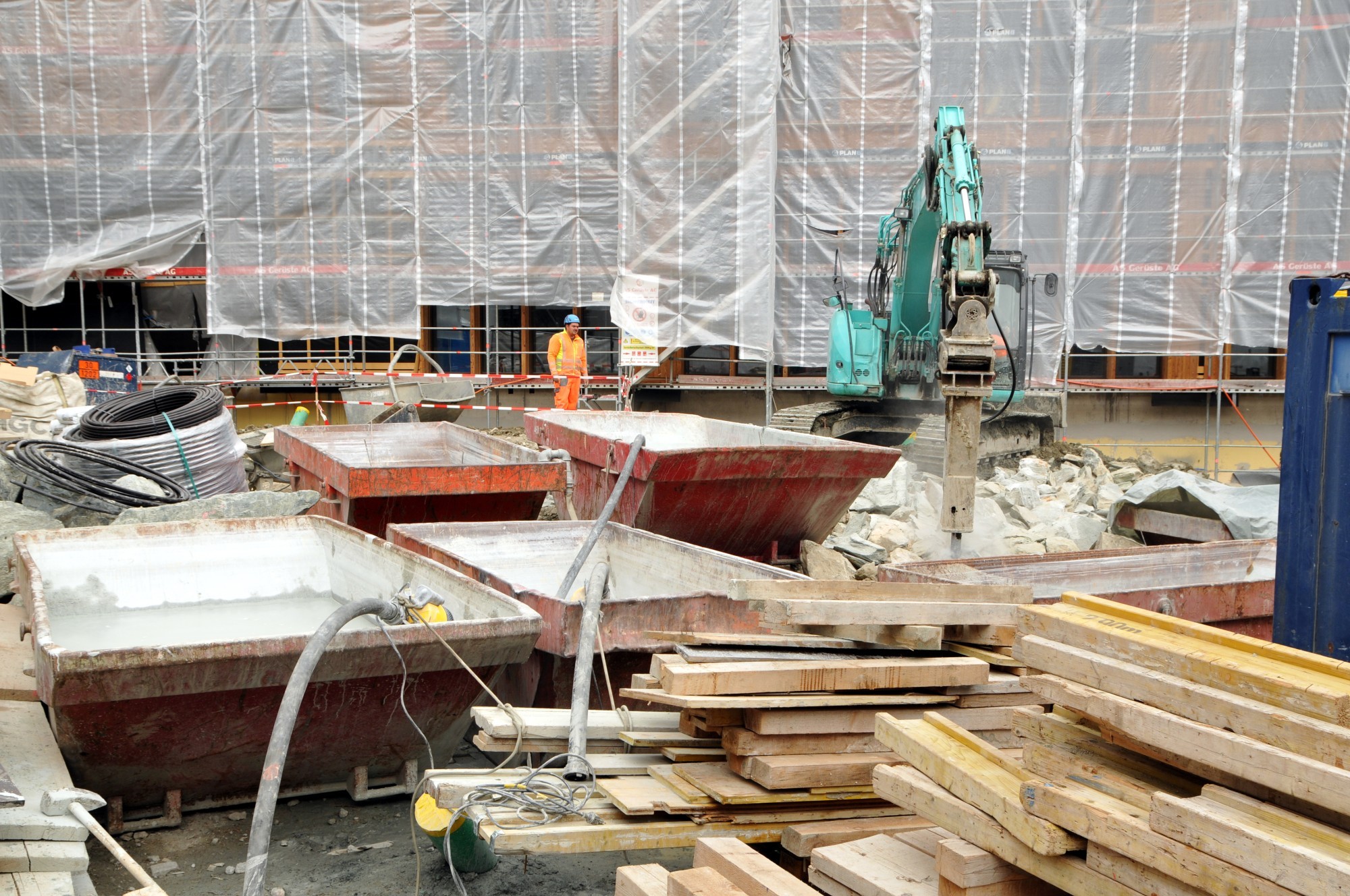
Quelle: Ben Kron
Der Bohrrückfluss bleibt in diesen Mulden stehen, bis sich genügend Schwebstoffe abgesetzt haben. Erst dann kann das Wasser zur Aufbereitung weitergeleitet werden.