Ein nachhaltiges Rezept für die Entsorgung von Asbest?
Seit zwei Jahren verfestigt die Solothurner Menz AG asbesthaltige Bauabfälle zu einem inerten Abfallstoff. Die Lösung: Mit einem speziellen Rezept werden die gefährlichen Fasern in Zementblöcke eingegossen, die man ohne Probleme in Endlagern entsorgen kann.
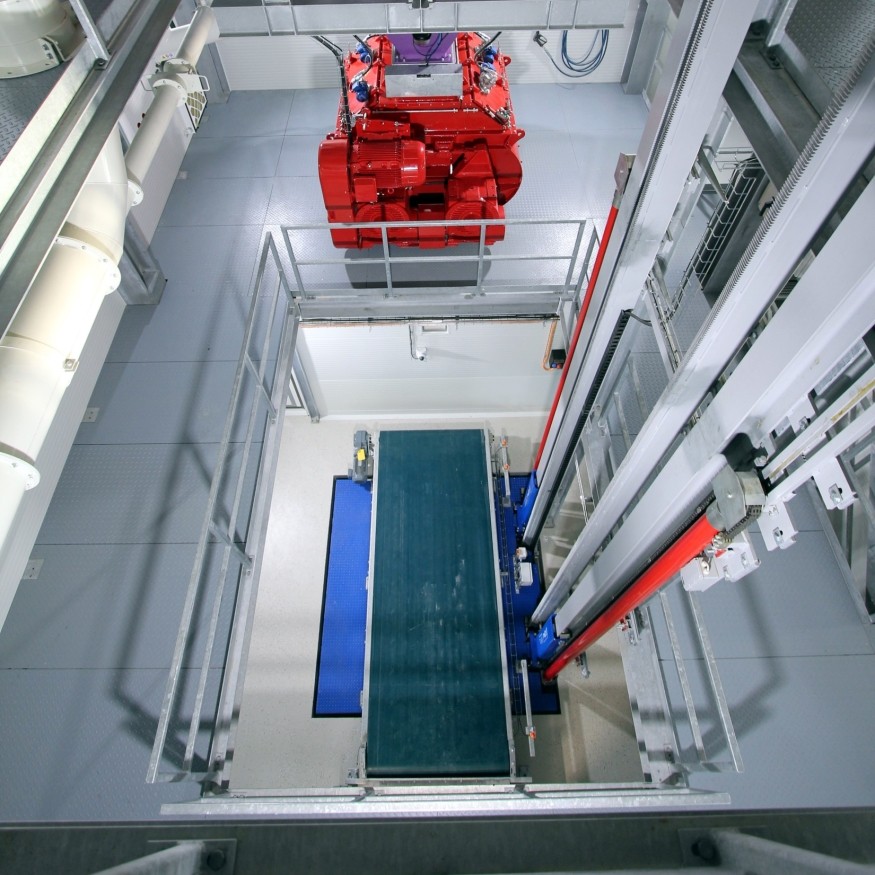
Quelle: Festex AG
Vom Förderband (unten) werden die Säcke hochgehoben, in den Brecher entleert, dort zerkleinert, und anschliessend wird das Material mit Zement, Wasser und Zuschlagstoffen zu einem dicken Brei vermengt.
Seit 1990 sind Asbestfasern in der
Schweiz verboten. Doch schon einige Jahre früher gerieten die mineralischen
Fasern unter Verdacht, Krebs verursachen zu können. So gab der Bund Mitte der
1980er Jahre eine Publikation heraus, worin auf die Gefahren von Asbest in
Schulhäusern und Sportanlagen hingewiesen wurde. Erste Gemeinden begannen
darauf, ihre betroffenen Gebäude und Anlagen zu sanieren.
Die Menz AG im solothurnischen Luterbach gehört zu den
Unternehmen, die schon damals solche Asbestsanierungen durchführten. «Wir haben
vor über dreissig Jahren Methoden und Schutzkonzepte erarbeitet, in
Zusammenarbeit mit dem arbeitshygienischen Institut in Neuenburg», erinnert
sich Firmeninhaber Christoph Menz. «Wir arbeiteten von Anfang an mit
Unterdruck, Schutzanzügen und speziellen Masken, so dass wir unsere Methoden im
Laufe der Zeit nur gering-fügig anpassen mussten.»
Deponieplatz wird knapp
Gar nichts geändert hat sich lange Zeit am Umgang mit dem rückgebauten, asbesthaltigen Material: Dieses wurde und wird in Plastiksäcke verpackt und auf Deponien vom Typ E gelagert, früher Reaktordeponien genannt. Diese Art der Endlagerung bringt vor allem dann grosse Probleme mit sich, wenn die Deponie eines Tages rückgebaut werden muss. Zudem ist der Platz auf solchen E-Lagerstätten in der Schweiz begrenzt; aktuell gibt es 24 ausgewiesene Deponien.
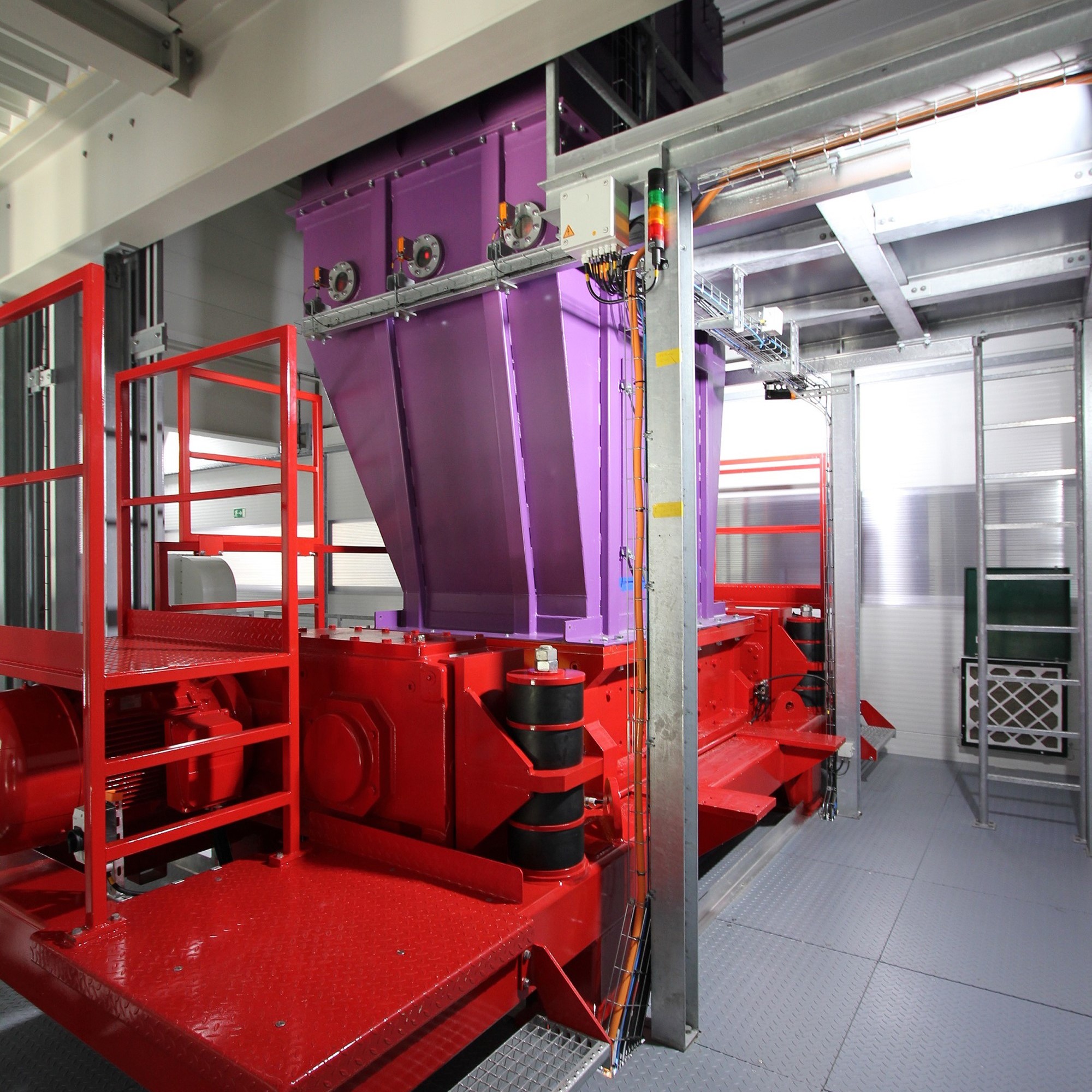
Quelle: Festex AG
Am Ende des Prozesses wird der Brei in Metallbehälter entleert, worin die Masse zu den endgültigen Zementquadern erstarrt.
Bei der Menz AG begann man deshalb vor einigen Jahren, eine
andere Lösung zu suchen. «Wir suchten nach einem Weg, wie wir asbesthaltigen
Abfall in einer sicheren Form der Nachwelt überlassen können, wie wir also die
Fasern in einem anderen Material binden und verfestigen können», sagt Menz.
Lösung ohne höhere Kosten
Es gab damals zwar bereits mehrere Technologien für den
Umgang mit Asbest: So wurde das Material eingeschmolzen, bei sehr hohen
Temperaturen in Spezialöfen verbrannt und verglast. «All diese Technologien
verursachen aber sehr hohe Kosten. Unser Ziel war es, eine Lösung zu fin-den,
die am Ende nicht wesentlich teurer ist, als die Endlagerung auf der Deponie»,
so Menz.
Also tüftelte man mit Zement als Bindemittel: Dieses ist
relativ günstig und wird in der Schweiz in grossen Mengen hergestellt. Dazu
experimentierte man mit einer Reihe von weiteren Zuschlagsstoffen und vorerst
mit asbestähnlichen, aber ungefährlichen Bauabfällen. «Das Know-how für diese
Entwicklung haben wir uns über unsere anderen Geschäftsfelder erworben», so
Menz. «Wir waren als Malergeschäft stets offen für weitere Aufgaben, etwa im
Bereich von Strahlarbeiten und Betonsanierungen. Dadurch haben wir regen
Kontakt und Austausch mit anderen Gewerben.»
Auf Inertstoff-Deponie lagerbar
So entwickelte man ein Rezept, mit dem sich die gefährlichen Fasern in einem soliden Zementblock verfestigen lassen. Dieser wiederum kann auf einer Deponie der Kategorie B, also einer Inertstoff-Deponie gelagert werden. Die Quader bleiben über einen langen Zeitraum hinweg solid, verlieren zwar Wasser, was aber keine Fasern freisetzt und die Festigkeit nicht beeinträchtigt.
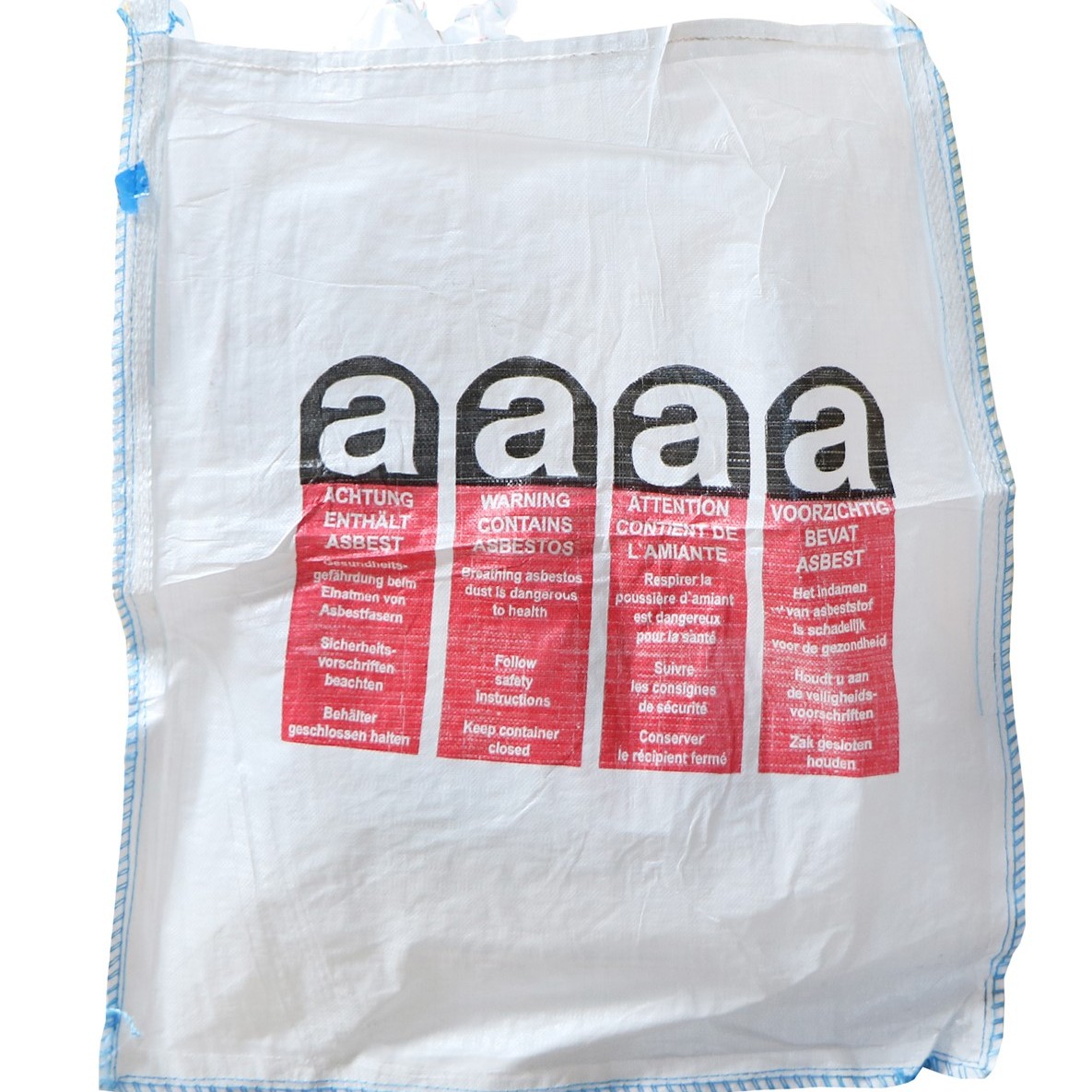
Quelle: bigbagstore.nl
Asbesthaltiges Material wird in solche Big Bags verpackt – und oft auch so auf Deponien eingelagert. Für die Anlage in Luterbach sind diese Säcke das Ausgangsmaterial.
Als das Rezept stimmte, baute man erst kleinere und später
grössere Anlagen, welche die Verfestigung der Fasern zu solchen Blöcken
vollautomatisch vornehmen sollten. Daneben arbeiteten die Entwickler der Firma
Menz eng mit dem kantonalen Amt für Umwelt zusammen. «Von dort erhielten wir
Unterstützung und man ging davon aus, dass eine Bewilligung für eine solche
Anlage möglich ist», sagt Menz.
Rechtliche Hürden ausgeräumt
Bedenken gegen das Projekt gab es anfangs aus Luzern von der Suva. Diese verwies auf die Chemiereduktionsverordnung, wonach Asbest grundsätzlich nicht weiterverarbeitet werden darf. Die Lösung aus dieser Sackgasse: Man konnte rechtsverbindlich festhalten lassen, dass die entwickelte Methode keine Weiterverarbeitung von Asbest darstellt, sondern eine Umwandlung von Abfallstoff in eine unbedenkliche Form.
Und da Asbestfasern in der Natur in Gestein gebunden vorkommen und in dieser Form ungefährlich sind, erwies sich das Einschliessen in Zement als nachhaltige Lösung. Damit hatte die Asbestverfestigung der Firma Menz von den Behörden grünes Licht. Am Firmensitz in Solothurn wurde eine Anlage errichtet, welche die Abfälle vollautomatisch verarbeitet. Diese wird von der Festex AG betrieben, einem Menz-Tochterunternehmen.
Stefan Röösli ist Bereichsleiter und für den Betrieb der Anlage verantwortlich: «Die Anlage funktioniert vollautomatisch, inklusive Reinigung nach jeder Charge, so dass im Normalbetrieb nie ein Mensch das Innere betreten muss.» Nur zur Revision, die alle drei Monate stattfindet, wird die Anlage betreten. Dies war eine Auflage zur Arbeitssicherheit der Suva, mit der man eng zusammenarbeitet. So ist das Unternehmen Mitglied der Sicherheits-Charta der Suva, was allerhöchste Standards voraussetzt.
Unterdruck schützt Umwelt
Die ganze Anlage läuft in einer luftdichten Einhausung und steht unter Unterdruck, so dass keine Luft entweichen kann. «Doch schon im Inneren ist die Anlage so konzipiert, dass gar keine Asbestfasern aus dem Produktionsprozess entweichen können», erklärt Röösli. Die Big-Bags und Säcke mit asbesthaltigem Rückbaumaterial werden an einer Doppel-Schleuse auf ein Förderband gelegt.
Von dort übernimmt die Anlage alle Arbeitsschritte: Erst wird das Material den Säcken entnommen, gebrochen und gemischt, dann mit Wasser angerührt und am Ende in Metallformen gegossen, die bei der Ausgabeschleuse herauskommen, mit den Asbestfasern sicher im Zement gebunden. Bei der Ausgabeschleuse ist der Unterdruck jeweils leicht geringer als in den vorangehenden Bereichen, so dass kein Staub in diesen letzten Sektor gelangen kann
Die gesamte Anlage wird rund um die Uhr von Sensoren überwacht, die bei einem Leck in der Unterdruck-Hülle sofort Alarm schlagen und tagsüber auch gleich die Anlage herunterfahren. Die Abluft reinigen Filter der Klassen H13 und H14. «Der Staub, der beim Bearbeiten entsteht, wird abgesaugt, gesammelt und der nächsten Charge wieder zugeführt, sodass wir ausser den Zementblöcken am Ende keinerlei Abfallmaterial verursachen», so Röösli.
Auch
das Wasser, das zum Spülen der Anlage verwendet wird, sammelt man und verwendet
es für die nächste Zementmischung. «Der Wasserverbrauch ist recht hoch und
liegt pro Charge bei 180 bis 200 Litern. Haben wir viel Gips im Rückbaumaterial,
können es sogar 300 Liter sein.» Den Stromverbrauch beziffert der
Bereichsleiter auf rund fünf Franken pro Charge.
Jedes Material verarbeitbar
Verarbeitet werden kann dabei fast jede Form von Rückbaumaterial. «Für die Anlage spielt es keine Rolle, ob das Material zu 100 oder nur zu ein bis zwei Prozent aus Fasern besteht», betont Menz. Das führt aber natürlich dazu, dass die Zementblöcke als Endprodukt im Volumen variieren. Für die optimale Mischung der Komponenten und das Timing ist der Anlagenführer verantwortlich.
Er kann auf Monitoren alle Arbeitsschritte im Inneren der Anlage überwachen. Dazu hat er auf seinem Bildschirm Zugriff auf alle Anlagenteile und kann die jeweiligen Werte und Mengen überwachen. «Die Anlage läuft zwar automatisch», erklärt er, «aber ich greife trotzdem regelmässig ein. Zum Beispiel hat das Material, das in die Anlage kommt, unterschiedliche Konsistenz, Gewichte und Volumen. Das kann ich nicht beliebig mischen, da sonst die Anlage Mühe hat und der Prozess länger dauert.»
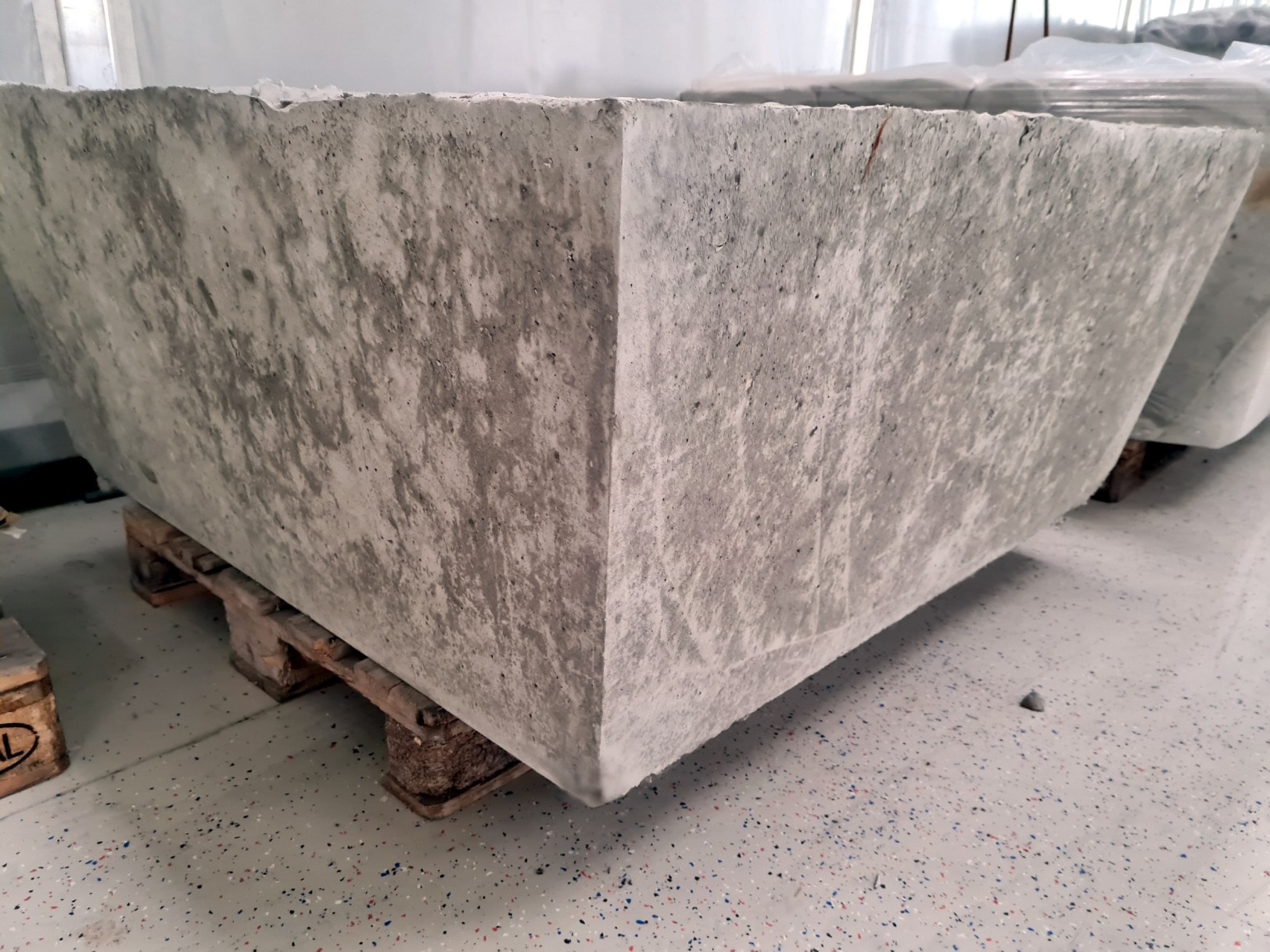
Quelle: Festex AG
Das äusserlich unspektakuläre Endprodukt des nachhaltigen Rezepts: 1,6 Tonnen schwere Zementblöcke, mit darin felsenfest eingeschlossenen Asbestfasern. Diese Blöcke können ohne Gefahr für die Umwelt auf die Deponie.
Von Hand erfolgt meistens auch das Ablassen der fertigen Mischung: «Im Durchschnitt dauert der Prozess pro Charge acht Minuten, aber mit den verschiedenen Ausgangsstoffen braucht es am Ende meistens etwas weniger oder mehr Zeit. Wir arbeiten hier, anders als etwa in einem Betonwerk, mit sehr unterschiedlichen und nicht homogenen Stoffen. Das macht das Mischen anspruchsvoll.» Der Anlageführer hat deshalb den Zementbrei im Auge und weiss wie ein guter Bäcker beim Teig, wenn dieser fertig ist. Am Ende des Prozesses stehen unterschiedlich hohe Quader der stets selben Grundform, jeweils 1,6 Tonnen schwer, mit eingegossenen Halterungen für den Transport.
2000 bis 3000 Tonnen pro Jahr
Die Anlage in Luterbach läuft seit über zwei Jahren und verarbeitet pro Jahr 2000 bis 3000 Tonnen asbesthaltiges Material, woraus rund 15 Volumenprozente mehr Abfall werden. In dieser Zeit mussten nur geringfügige Modifikationen vorgenommen werden. Menz: «Das System hat sich bewährt. Wir können heute damit sämtlichen Asbestabfall verarbeiten, von uns und von Drittfirmen.» Von den Deponien habe man die positive Rückmeldung, dass das Material sehr gut einbaubar und problemlos sei.
«Wir können die Anlage noch deutlich höher fahren», erklärt der Firmeninhaber. «Im Moment arbeiten wir einschichtig, haben aber schon heute damit den Break Even erreicht.» Für die Zukunft will man deutlich mehr Material verarbeiten und sich als Alternative zu E-Deponien etablieren. «Der Platz in den Deponien ist beschränkt, und wir haben eine Lösung für das Problem.»
Der Bedarf für Asbestentsorgung wird hoch bleiben. Menz schätzt, dass die Sanierungsspitze noch nicht erreicht ist. «Es wurden in vielen Materialien Asbestfasern festgestellt, etwa in Spachtelmassen bei Leichtbauwänden, in Grund- und Deckenputzen. Hier kommen noch viele Sanierungen und damit sehr grosse Volumen an asbesthaltigem Material auf uns zu.»
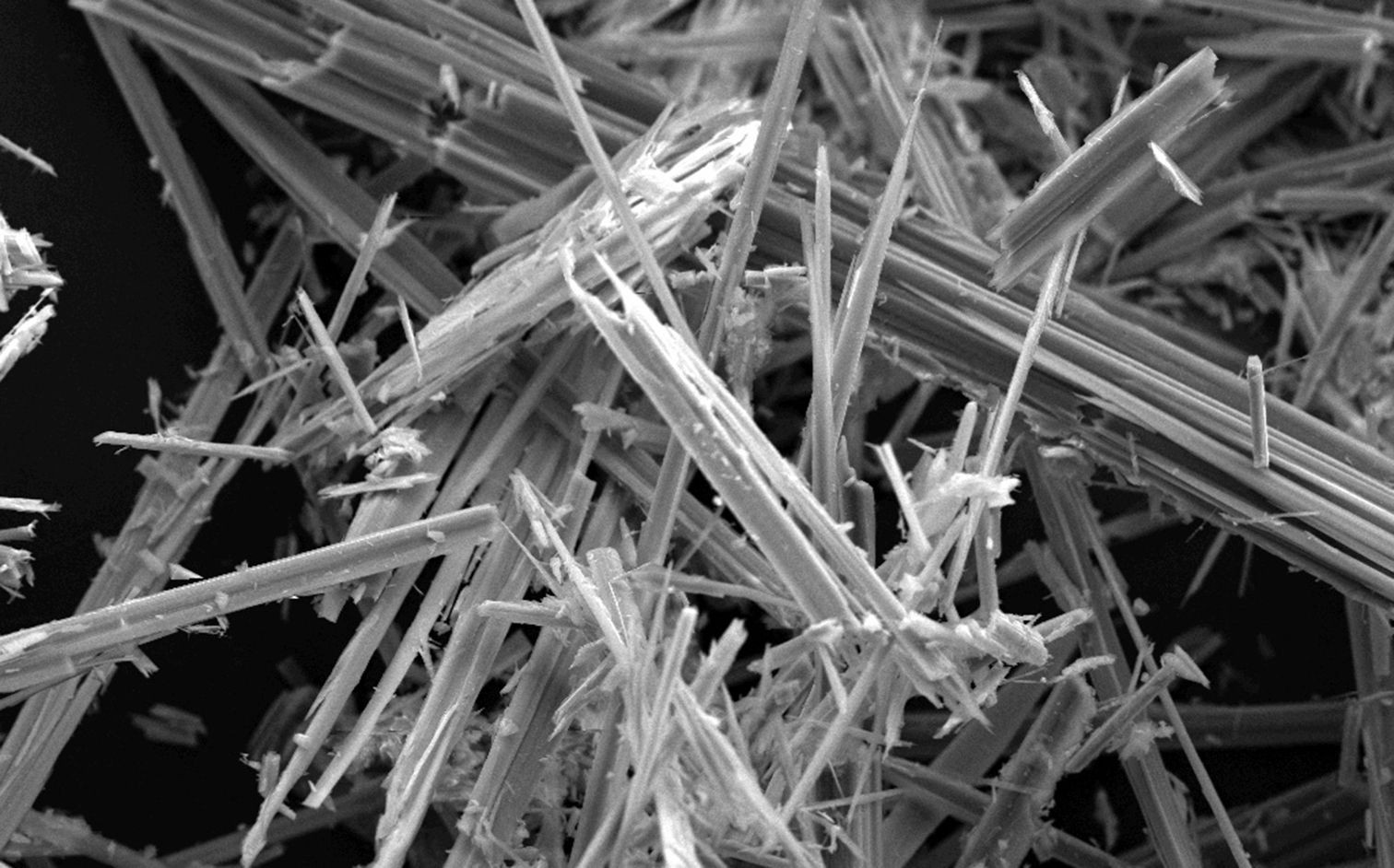
Quelle: Gemeinfrei
Elektronenmikroskopische Aufnahme von Asbestfasern. (Symbolbild)