CO2-Speicherung im Beton: Richtig Gas geben bei der Dekarbonisierung
Die Versteinerung des klimaschädlichen Kohlendioxids im Betongranulat von aufbereitetem Abbruchmaterial hat für die Bauindustrie grosses Potenzial. Ein Grossteil der CO2-Emissionen liesse sich kompensieren. Das Verfahren eines ETH-Spin-offs verbessert sogar die Materialeigenschaften des Betons. Auf einem der schweizweit grössten Recyclingwerke wird die Anlage getestet.
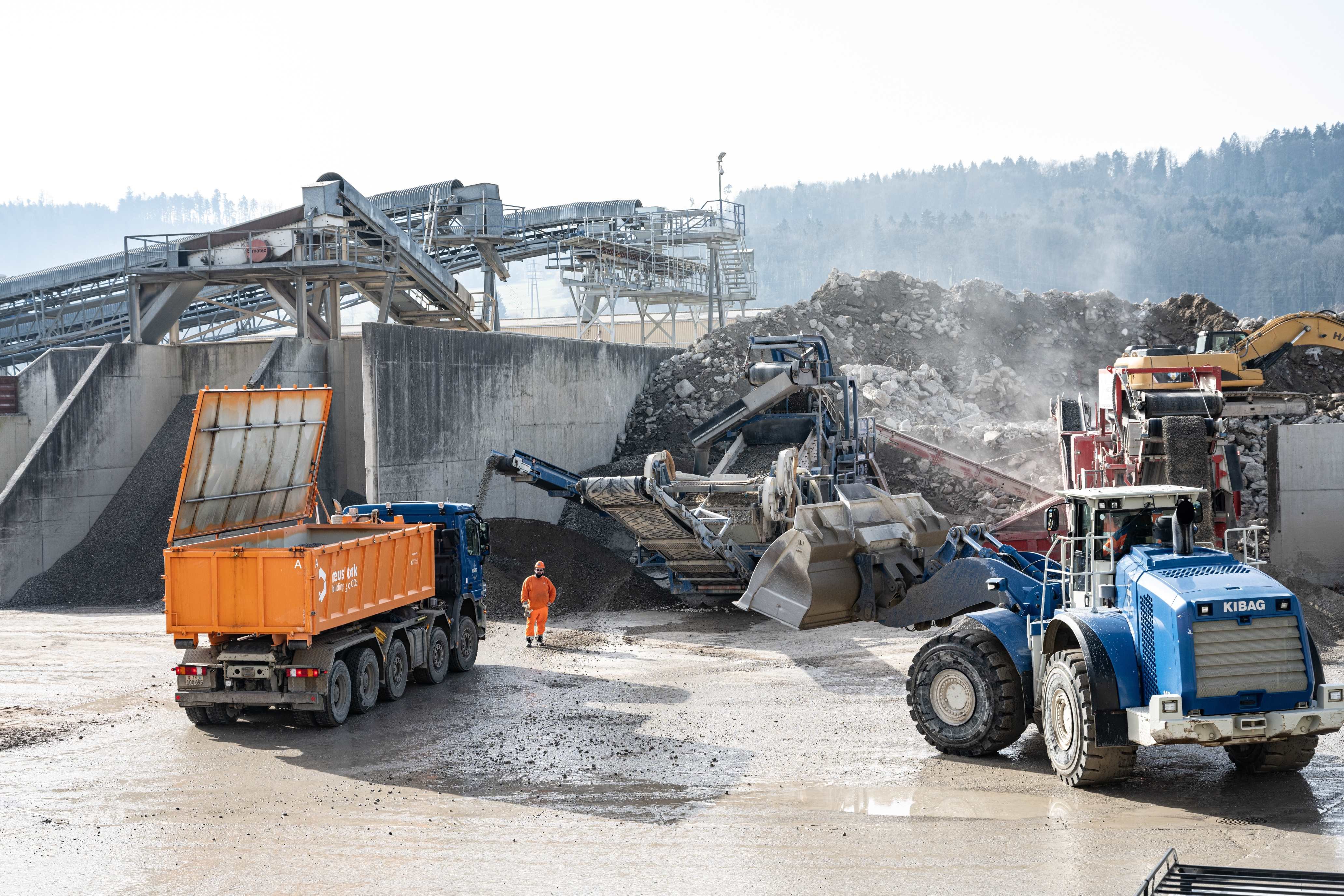
Quelle: Kibag Bauleistungen AG
Direkt von der Aufbereitungsanlage der Kibag befüllt der Radlader den Container mit 15 Kubikmeter Betongranulat.
Die Konzentration an Kohlendioxid in der Atmosphäre erhöhte
sich seit den ersten Industrialisierungswellen im vorletzten Jahrhundert
stetig. Die Klimakrise ist ein Fakt. Die wissenschaftlichen Erkenntnisse über
die Erderwärmung sind längst bekannt. Über die Folgen der Klimakrise ist sich
auch die Wirtschaft im Klaren. Das revidierte CO2-Gesetz, das im Juni zur
Abstimmung gelangt, findet breite Unterstützung in der Wirtschaft. Der Pariser
Klimavertrag verpflichtet die Schweiz zudem, bis 2030 die Emissionen um die
Hälfte zu senken. Mit zwei Stossrichtungen ist die Dekarbonatisierung daher
wichtiger Bestandteil der Massnahmen. Einerseits heisst das, weniger CO2 in die
Atmosphäre zu blasen, anderseits das schädliche Klimagas zu binden. Den zweiten
Weg beschreitet die Neustark AG mit einem neuen Verfahren.
«Es bestand von Anfang an der Anspruch, an
Zukunftstechnologien zu forschen, um CO2 speichern zu können. Gleichzeitig wollten
wir Lösungen erarbeiten, die sich heute schon einsetzen lassen», sagt Valentin
Gutknecht, Mitgründer und CEO des ETH-Spin-offs. Dabei sind Dekarbonatisierung
und Karbonatisierung sozusagen die zwei Seiten der gleichen Medaille. Die
Begriffe zeigen, wie naheliegend die Lösung des Jungunternehmens für die
Bauindustrie ist, handelt es sich beim Prozess der natürlichen Karbonatisierung
doch um einen gängigen Begriff der Bauchemie. Das Phänomen ist schon lange
bekannt und auch gut erforscht.
Altes Phänomen neu gedacht
Auf dem Kibag-Areal in Regensdorf ZH, einem der schweizweit
grössten Recyclingwerke für Bauschutt und Abbruchmaterial, steht seit letzten
Sommer die Anlage der Neustark AG, es ist weltweit die erste und einzige ihrer
Art. Mit der mobilen Pilotanlage, bestehend aus drei Containern, soll das
Verfahren unter realen Bedingungen im Produktionsprozess für Frischbeton
getestet werden. Zum einen geht es um betriebswirtschaftliche Aspekte der
Prozessgestaltung, zum anderen um die Optimierung der Anlage für die CO2-Speicherung.
Das Neustark-Verfahren beschleunigt den Mineralisierungsprozess massiv und
vervielfacht dadurch die durchschnittliche CO2-Aufnahme. Zentraler
Prozessschritt des Verfahrens: die Karbonatisierungsfront.
Bedingungen sind hochreaktiv
Dazu wird einer der beiden Container mit 15 Kubikmetern aufbereitetem Betongranulat bis zur Hälfte befüllt und danach luftdicht verschlossen. In einem zweiten Schritt wird CO2 in den Behälter gepumpt. Die CO2-Beflutung schafft hochreaktive Bedingungen, sodass bei Kleinstpartikeln aus Zement der Mineralisierungsprozess in Gang kommt. Dabei wird Calciumhydroxid unter Bindung von CO2 in Calciumcarbonat umgewandelt. Es ist die Umkehr des chemischen Prozesses, wie er bei der Zementherstellung abläuft.
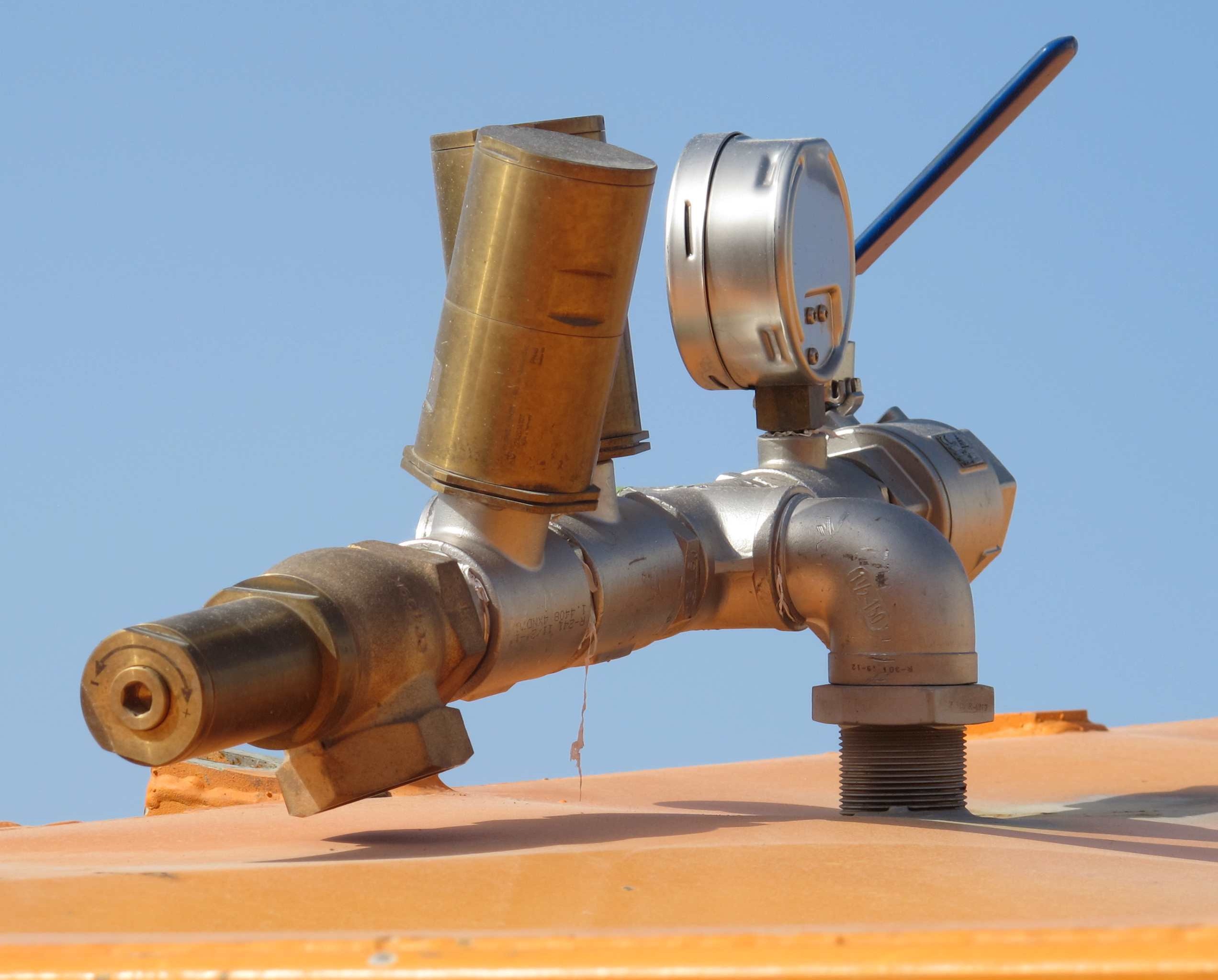
Quelle: Stefan Schmid
Der chemische Prozess setzt physikalische Kräfte in Gang, die mit einem Druckausgleichsystem unter Kontrolle gehalten werden müssen.
Aufgrund der chemischen Reaktion im Behälter entwickeln sich
gewaltige physikalische Kräfte, weil das Gasvolumen viel grösser ist als der
entstehende Kalkstein. Zum Vergleich: CO2 vom Volumen eines Luftballons wird in
ein paar Gramm Kalkstein umgewandelt. Ein Vakuumbrecher regelt daher den
Unterdruck im Behälter. Über ein Injektionssystem im Innern wird
sichergestellt, dass die gesamte Masse des Granulats durchflutet wird und das
Gas den Weg zu den Kleinstpartikeln findet. Dabei gilt: Je feiner das Granulat
ist, desto grösser ist gesamthaft die reaktive Oberfläche.
Klimaneutralen Beton herstellen
Zudem werden kleinste Zementpartikel von der
Karbonatisierungsfront schneller durchdrungen als grössere Brocken. Der Druck
für die Zufuhr von CO2 und die Siebkurve des Granulats sind daher zwei wichtige
Regelgrössen. Ein bis zwei Stunden dauert es, bis die Karbonatisierungsfront
die Kleinstpartikel durchdrungen hat. Dann schwächt sich die Reaktion ab, doch
ist in dieser Zeit bereits ein Sättigungsgrad von rund 80 Prozent erreicht.
Grössere Zementbrocken sind noch nicht vollständig in Kalkstein umgewandelt.
Bis eine maximale Sättigung resultiert, dauert der Prozess entsprechend länger.
95 bis 99 Prozent des verwendeten CO2 werden nachgewiesenermassen zu Kalkstein
umgewandelt.
Zehn Kilogramm CO2 pro Kubikmeter Frischbeton lassen sich
mit dem Verfahren bei der Testanlage speichern. Doch der Effekt kann
vervielfacht werden. «Einem Kubikmeter Beton kann schliesslich so viel
gespeichertes CO2 zugeführt werden, dass die Emissionen, die mit der Zementproduktion
entstehen, komplett rückgängig gemacht werden können. Je nach Betonmischung
können dann pro Kubikmeter zwischen 150 und 250 Kilo CO2 gespeichert werden.
Damit wäre es dann ein klimaneutraler Beton», sagt Betriebswirt Gutknecht. Nach
dem Umwandlungsprozess kann das Granulat zu Frischbeton weiterverarbeitet und
danach direkt verbaut werden.
Ausstoss und Speichereffizienz sind für Betonwerke zwei
Optimierungsgrössen. Bei 99 Prozent ist der Verlust kleiner, die Kapazität der
Anlage aber leicht reduziert. Um die Massenzunahme des Granulats zu messen,
steht der Container auf einer Waage. Das Resultat wird durch die Messung des
Gasdurchflusses validiert.
Bessere Qualität des Betons
Die Siebkurve des Granulats wurde bisher wenig verändert, für Recyclingbeton liegen die Zuschlagsstoffe oft zwischen 0 bis 16 und 0 bis 22 Millimeter. Allenfalls liesse sich das Granulat feiner brechen, um mehr reaktive Oberfläche zu schaffen. Betonwerke müssen daher ein Optimum finden zwischen dem Aufwand fürs Brechen und der CO2-Speicherung.
Der nach dem Neustark-Verfahren hergestellte Beton
entspricht zu 100 Prozent den bestehenden Leistungsnormen. Weil der
eingelagerte Kalkstein die Poren schliesst, resultiert sogar eine bessere
Qualität des ausgehärteten Betons hinsichtlich Druckfestigkeit. Bei gleichen
Eigenschaften kann der Zementgehalt des Betons darüber hinaus in vielen Fällen
leicht reduziert werden.
Für die Bauindustrie eröffnet sich mit dem Verfahren die
Möglichkeit, die Dekarbonatisierung breitflächig voranzutreiben. Denn allein
die Zementproduktion verursacht sieben Prozent der weltweiten CO2-Emissionen
oder doppelt so viel wie der gesamte weltweite Flugverkehr. Insgesamt emittiert
die Zementproduktion weltweit pro Jahr rund 2,5 Milliarden Tonnen CO2. Laut
Schätzungen von Wissenschaftlern könnten bis 2050 jährlich rund 500 Millionen
Tonnen CO2 gespeichert werden. «Das Abscheiden von CO2 aus der Luft ist
zentral, um sich das im Beton gespeicherte CO2 anrechnen zu lassen», sagt
Gutknecht. Was mit dem Neustark-Verfahren im Kleinen beginnt, könnte sich zu
einem gigantischen Hebel entwickeln. Denn durch die Einlagerung des Klimagases
entsteht zugleich eine sogenannte CO2-Senke. Diese wiederum liesse sich mit
CO2-Umweltzertifikaten kombinieren. Und mit Gütesiegel produzierter
Neustark-Beton könnte sowohl öffentliche oder private Bauherrschaften
veranlassen, mehr für die Dekarbonatisierung zu tun. Auch bei der
Immobilienvermarktung könnte das Gütesiegel für die Profilierung des Angebots
künftig eine Rolle spielen. Mit der konsequenten Wiederverwertung von
Abbruchmaterial können zudem Primärstoffe geschont werden, was insbesondere für
Grossagglomerationen wie Zürich gilt. Denn für Betonproduktionsunternehmen wie
die Kibag wird es wegen des Widerstands der Bevölkerung immer schwieriger, neue
Kiesabbaugebiete zu erschliessen.
«Positive Bilanz»
Durch die Entfernung von CO2 aus der Atmosphäre und die anschliessende Speicherung können sogenannte Negativemissionen und damit Klimapositivität realisiert werden. Beim Gesamteffekt der CO2-Speicherung sind allerdings noch graue Emissionen zu berücksichtigen, die bei der Gasverflüssigung mit Strom, dem Transport sowie dem Betrieb der Anlage entstehen. Drei bis fünf Prozent sind daher pro Tonne eingespartes CO2 in Abzug zu bringen, wie eine Analyse der ETH Zürich ergab. «Es ist aber ganz klar eine positive Bilanz», bekräftigt Gutknecht.
Das verflüssigte CO2 wird künftig von der
Abwasserreinigungsanlage Region Bern bezogen, bei der die Neustark AG im April
eine Abscheide- und Verflüssigungsanlage in Betrieb nimmt. Das CO2 entsteht
dort bei der Biogasanlage durch die Vergärung von Biomasse. Es wird direkt beim
Kamin abgefangen, anstatt es in die Atmosphäre entweichen zu lassen.
Stationäre Grossanlagen geplant
Derzeit mineralisiert die mobile Pilotanlage pro Stunde rund
20 Tonnen Betongranulat. Pro Container liegt die Kapazität bei 100 Tonnen pro
Tag. Mobile Anlagen könnten nach Optimierungen bei kleinen und mittelgrossen
Betonherstellern künftig dauerhaft zum Einsatz kommen. «Der Markt ist bereit
dafür. Dann braucht es betriebsspezifisch ideale Lösungen, um den Prozess in
bestehende Anlagen von Betonwerken zu integrieren», sagt Gutknecht. Die
effizienteste Lösung für die Speicherung von CO2 aber könnten stationäre
Grossanlagen sein, indem man den Versteinerungsprozess in Lagersilos ablaufen
lässt.
Komplexes Verfahren
Auf die Idee, die Dekarbonatisierung mit neuen Anwendungen
zu verbinden, kam Gutknecht als Marketing Manager bei Climeworks, einem
Unternehmen, das Lösungen zur Abscheidung von CO2 aus der Luft anbietet. Dabei
wurde er sich bewusst, dass die Abscheidung mittels Grossanlagen und die
Entsorgung von CO2 in den Untergrund schwierig zu bewerkstelligen ist.
Insbesondere, weil dadurch kein direkter wirtschaftlicher Mehrwert entsteht.
Der Ansatz, die CO2-Problematik mit einem wirtschaftlichen
Mehrwert beim Abbruchmaterial zu verbinden, konkretisierte sich dann 2017 nach
Gesprächen mit Betreibern von Betonwerken. Damals hat sich auch Mitgründer
Johannes Tiefenthaler, der an der ETH Maschinenbau und Verfahrenstechnik
studierte, im Rahmen seiner Masterarbeit intensiv mit dem Thema befasst. Es war
dann nur eine Frage der Zeit, bis sich beider Wege auf dem gemeinsamen
Betätigungsfeld kreuzten.
Mit der Firmengründung war auch der selbstgewählte Auftrag klar. «Wir wollten Bewegung in die Sache bringen», sagt Gutknecht beim Gespräch auf dem Kibag-Areal. Operativ tätig ist die Gesellschaft seit 2019, wobei Gutknecht für die kommerziellen und Tiefenthaler für die technischen Belange zuständig ist. Bei der Neustark AG sind mittlerweile neun Mitarbeiter tätig.
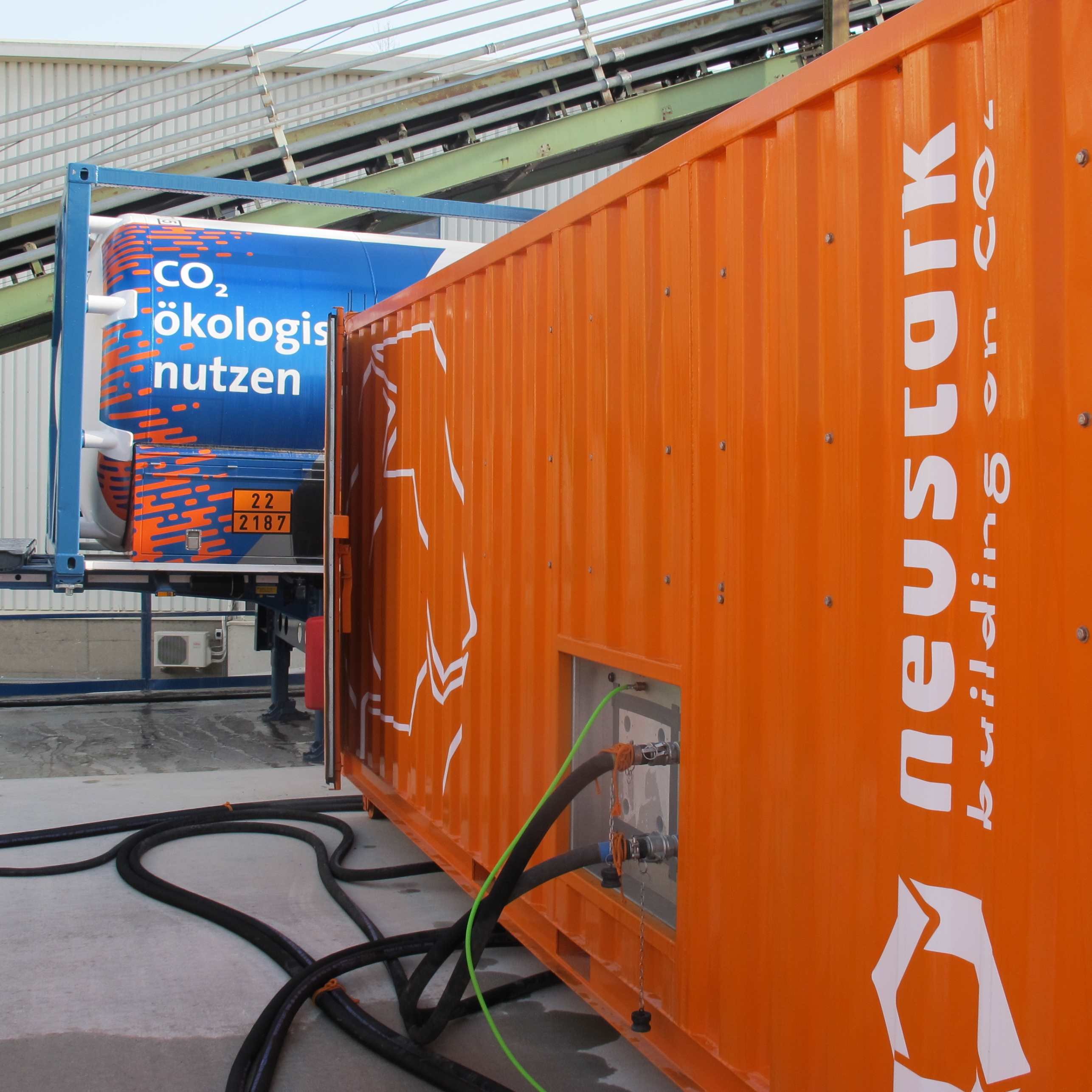
Quelle: Stefan Schmid
Dieser Tank enthält 20 Tonnen flüssiges CO₂. Damit lassen sich 2000 Kubikmeter Frischbeton herstellen.
Die kommerzielle Umsetzung des Gesamtkonzepts in eine mobile
Anlage umfasst eine grosse Bandbreite von technischen Herausforderungen wie die
Gewinnung und Bereitstellung von Flüssiggas, Betonrezepte sowie
verfahrenstechnische und materialwissenschaftliche Aspekte. Schliesslich
erfordert auch die CO2-Bilanzierung über den gesamten Prozess einen genauen
Nachweis der Mineralisierung und damit des Dekarbonatisierungseffekts.
Internationale Ambitionen
Die Anschubinvestitionen im Umfang von insgesamt «wenigen
Millionen Franken» für die Entwicklung der Anlage wurden zu Beginn aus
Fördergeldern des Bundesamts für Umwelt sowie der Klimastiftung Schweiz und von
Schweizer Privatpersonen finanziert. Es handelt sich um Investments mit
langfristiger Perspektive, aber ohne strategische Interessen in der Baubranche.
Venture Capital und Fonds sind zurzeit nicht vertreten. Tiefenthaler und
Gutknecht halten die Aktienmehrheit am Unternehmen. In der Schweiz kann das
Jungunternehmen die Weiterentwicklung der Anlagen sowie der Investitionen in
den Marktaufbau aus eigenen Mitteln finanzieren. Mittelfristig hat die Neustark
AG aber internationale Ambitionen. Für die Wachstumsfinanzierung und die
internationale Marktentwicklung könnte daher laut Gutknecht eine weitere
Finanzierungsrunde erforderlich sein. Das Patent für das Verfahren und die
Anlagetechnik ist hinterlegt, auch für die Erschliessung der europäischen
Märkte. Eine Option gewährt in weiteren Absatzgebieten patenrechtlichen Schutz.
Für die rasche Marktbearbeitung sind laut Gutknecht Partnerschaften mit Unternehmen in anderen Ländern denkbar. Und er betont mit Blick auf die Unternehmensstrategie: «Wir wollen ein von Anbietern unabhängiges Massenprodukt schaffen, das flächendeckend Anwendung finden kann.» Der Erfolg des Geschäftsmodells dürfte auch künftige Generationen interessieren. Denn es könnte sich um eine ökologische Pionierleistung handeln.
Nachgefragt bei Valentin Gutkneckt
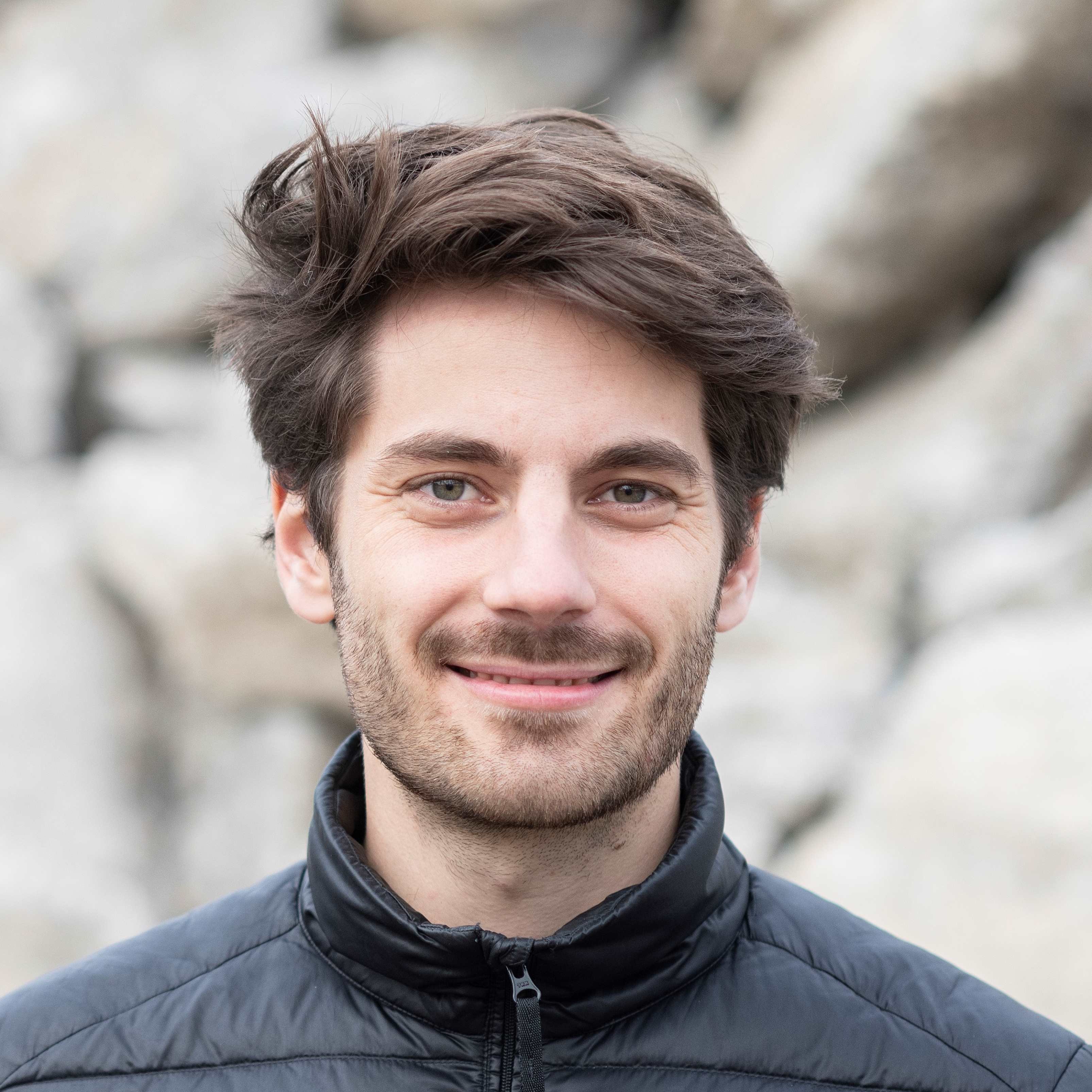
Quelle: zvg
Valentin Gutknecht ist Mitgründer und CEO der Neustark AG.
Was ist das Ausgangsmaterial für das Granulat?
Der Prozess funktioniert nur mit Abbruchmaterial und nicht mit primären Zuschlagsstoffen. Wir verwenden Zementrückstände und -abfälle, was die Wiederverwendung bei der Betonproduktion vereinfacht. Das Betonwerk kann entscheiden, wie hoch der Anteil von behandeltem Betongranulat im Frischbeton ist. Das ist sehr ortsabhängig. Beispielsweise gibt es in Zürich viel Betonrückbau und wenig Kies. Da macht es Sinn, bei der Betonproduktion höhere Recycling-Anteile zu fahren. In ländlichen Gebieten kann das anders sein. Wir versetzen den Betonrückbau lediglich mit CO2, der Rest ist die Kernkompetenz der Betonwerke.
Zehn Kilogramm CO2 lässt sich mit dem Neustark-Verfahren pro Tonne Frischbeton speichern. Sie gehen von einer Vervielfachung der gespeicherten Menge aus. Wie ist das möglich?
Wir haben eine neue Technologiegeneration entwickelt, die im Labor schon funktioniert und diesen Sommer als Ergänzung zur bestehenden Lösung im grösseren Massstab getestet wird. Es handelt sich um ein zweistufiges Verfahren für die Feinfraktion von Brechsand. Zuerst werden Zementanteile vom Primärsand getrennt. Danach lässt sich mit dem Zement hochreiner Kalk herstellen. Damit kommen wir sehr nahe ans theoretische CO2-Bindepotenzial.
Der Frischbeton ist zwar teurer, aber es gibt Vorteile bei den Materialeigenschaften. Können die Kosten damit ausgeglichen werden?
Die Preise für den Beton machen nicht wir. Die Mehrkosten betreffen vor allem die Handhabung der mobilen Anlage sowie die Abscheidung und den Transport des flüssigen Kohlendioxids. Unser Ziel ist es, stationäre Lösungen möglichst kostenneutral anbieten zu können und Mehrkosten optional über CO2-Zertifikate abzuwälzen.
Kann der Beton überall verwendet werden?
Die Betonsorten, bei denen Neustark zur Anwendung kommen kann, machen bei vielen Werken etwa 80 Prozent des Ausstosses aus. Ein Hochbauprojekt kann damit komplett umgesetzt werden. Der Tiefbau kann in einem zweiten Schritt beliefert werden. Alles, was sich mit Recycling-Beton machen lässt, geht auch mit der Neustark-Lösung.
Kommen künftig vor allem stationäre Anlagen zum Einsatz?
Es ist sehr abhängig vom Betrieb. In vielen Fällen macht eine stationäre Anlage Sinn. Bei Unternehmen mit verschiedenen Standorten kann die mobile Lösung die bessere sein. Mit Varianten können wir die unterschiedlichen Kundensegmente abdecken.
Valentin Gutknecht ist Mitgründer und CEO der Neustark AG.